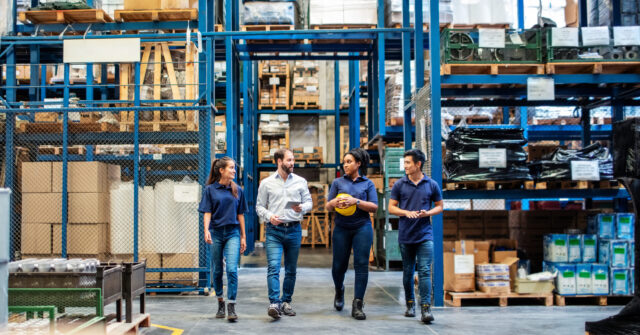
Implemente a disciplina de planejamento de recursos no armazém
Em um ambiente logístico em constante transformação, uma gestão ágil e precisa dos recursos no armazém é essencial para manter…
Generix é nomeada no 2025 Gartner® Magic Quadrant™ para Warehouse Management System (WMS) pelo sétimo ano consecutivo. Veja o comunicado de imprensa
A lógica da fase de armazenamento também se aplica à fase de separação. Nos armazéns tradicionais ou áreas de armazém, a separação é praticada na parte inferior do suporte: os slots reservados estão localizados no alto com paletes cheios, enquanto os slots inferiores são ocupados por paletes a serem retirados individualmente ou pacote por pacote.
Para maximizar o desempenho da separação, a correlação entre demanda e organização é fundamental no Sistema de gerenciamento de armazém (WMS). E o sistema de gestão de picking deve estar totalmente adaptado ao tipo de venda.
Para isso, o WMS irá propor, portanto, gerenciar os slots de preparação picking de forma “fixa” ou “temporária”. Em todos os casos, esses métodos de gestão permanecem complementares para adequar as operações às necessidades do mercado. É por isso que o picking “temporário” pode se tornar “fixo”, por exemplo, quando a demanda associada ao produto diminui ao longo dos dias ou das estações.
O picking fixo, particularmente adequado a uma organização de tipo linear, está associado a um percurso de preparação correspondente aos requisitos lógicos do tráfego nos corredores. Seu objetivo é otimizar os movimentos ou a constituição do suporte de preparação, ou o layout na bandeja ou na embalagem.
Isso permite, em última análise, evitar uma quebra no ritmo de carregamento no final do processo de preparação ou na chegada às instalações do cliente. Ou seja, desde o início priorizamos a preparação de um pedido em um único pacote, na medida do possível. Isso evita ter que embalar os pedidos novamente no final do processo de preparação ou enviá-los em dois pacotes, quando um seria suficiente.
A criação dos circuitos é definida pelo gestor de estoque de acordo com a necessidade do cliente. Respeita as regras relacionadas aos produtos: categoria, família, peso/volume, rotação, etc. No entanto, uma infinidade de combinações possíveis pode ser utilizada para otimizar sua constituição e promover sua complementaridade. É então que os algoritmos assumem sua importância no WMS, de modo a dar visibilidade ao gestor sobre o conjunto estratégico de carga/capacidade.
A etapa final: um caminho é estabelecido com base na análise dos dados relativos ao ciclo de vida do armazém, combinando o espaço disponível e o tipo de produto, dependendo da demanda. Quando os produtos estiverem armazenados no recebimento, usaremos outros cálculos para propor localizações de reserva o mais próximo possível do picking correspondente a cada referência.
Com o picking temporário ou “sob restrição”, recalculamos a implementação dos processos de picking dinamicamente durante o processamento de um ciclo de separação considerando as seguintes dificuldades:
Os algoritmos serão então configurados para implementar processos de picking que correspondam a cada referência da maneira mais adequada. Essa abordagem é muito eficaz para gerenciar grupos de referência de produtos relativamente pequenos, que estão em alta demanda por um período limitado. É o caso, por exemplo, do lançamento de uma nova coleção ou de uma oferta especial.
“Batch picking” ou massificação é um método de preparação de pedidos que se caracteriza pelo picking simultâneo de várias unidades com o mesmo código SKU para diferentes pedidos.
Especificamente, o preparador utiliza um carrinho de preparação no qual serão colocados “n” recipientes correspondentes a “n” pedidos diferentes. Ele poderá então distribuir a mesma referência em vários pedidos no mesmo ponto de retirada, minimizando assim seus movimentos. Para ajudar o preparador, um algoritmo calculará a divisão das tarefas para encontrar o método ideal de agrupá-las.
Este princípio é particularmente utilizado em e-commerce e setores têxteis que lidam com muitos pedidos pequenos (entre 1 e 3 peças em geral).
Podemos distinguir quatro tipos principais de tarefas para um operador de empilhadeira:
Essas missões podem ser combinadas ou cruzadas. Quando este é o caso, usamos o termo inglês interleaving.
Uma grande fonte de produtividade está na combinação de tarefas de armazenamento com tarefas de remoção de paletes. Na maioria das vezes, combinamos duas missões com pontos de entrega e coleta no mesmo corredor. Essas estratégias são particularmente eficazes nas chamadas áreas de armazenamento de “corredor muito estreito” (VNA para very narrow aisle) porque as empilhadeiras “tridi” (turret truck) usadas são mais lentas. Também são absolutamente cruciais ao usar Veículos Autoguiados (AGVs – Automated Guided Vehicle) cujas velocidades de deslocamento são lentas.
Também é possível calcular o estabelecimento das tarefas de acordo com um algoritmo de cálculo de distância. Esta funcionalidade é implementada configurando uma calculadora de distância. Isso consiste em estabelecer pontos de referência e ligações entre corredores de armazenagem para calcular a duração do percurso entre dois pontos de armazenagem, que podem estar localizados em corredores diferentes.
A triangulação é um método usado para medir distâncias em escala humana. Este é um processo de determinar uma distância calculando o comprimento de um lado de um triângulo e medindo dois ângulos desse triângulo usando entidades trigonométricas. O WMS inspira-se nele para aplicá-lo à gestão de armazéns e, assim, otimizar as viagens aplicando os caminhos mais diretos possíveis.
A triangulação é ideal em um contexto de radiofrequência. De fato, os cenários garantem a geração automática de tarefas por triangulação para operadores de empilhadeiras ou transportadores. Neste caso, os algoritmos WMS funcionarão com base em vários elementos:
O WMS também sabe calcular uma atribuição inteligente de docas em dois momentos-chave.
Com este modo de operação, o WMS poderá sincronizar fluxos de diferentes tipos (mono ou multipedidos, etc.). Isso permitirá atribuir dinamicamente uma doca de carregamento final ao validar os suportes no final do processo de preparação. O algoritmo terá então em conta o estado de congestionamento das docas ao mesmo tempo que verifica os critérios de consistência (clientes, datas de entrega, pedidos).
Também utilizamos métodos baseados em algoritmos para encher os caminhões da forma mais completa possível. Este trabalho é feito na maioria das vezes em colaboração com o TMS.
O conceito de cross-docking consiste em redistribuir os produtos no recebimento diretamente para uma doca de embarque sem passar pela fase de armazenamento. Os algoritmos do WMS podem operar usando duas tabelas. No caso de armazéns muito longos, que não sejam projetados como plataformas de cross-docking, deve ser dada prioridade à atribuição inteligente de docas de recebimento e/ou expedição, de forma a aproximá-las e, assim, minimizar as distâncias de deslocamento.
No caso de referências de produtos no recebimento que também estão em estoque, o WMS pode implementar algoritmos mais sofisticados que levarão em consideração vários parâmetros. Ou seja: podemos atender uma necessidade “espontânea” utilizando um palete recebido na doca. O sistema também está autorizado a ser utilizado na doca para evitar uma sucessão de transferências diferentes (o objetivo é minimizar as “rupturas de carga”). Neste caso, podemos decidir não respeitar a ordem FIFO (First In First Out). O sistema verifica o cumprimento das datas de vencimento e dos “contratos data”.
Em um ambiente logístico em constante transformação, uma gestão ágil e precisa dos recursos no armazém é essencial para manter…
Navegar no complexo labirinto do gerenciamento de recursos e cumprir prazos rigorosos é um desafio antigo enfrentado pelos gerentes de…
Em 2025, a supply chain continua sua evolução rumo à “Logística 4.0”, inspirada na Indústria 4.0. Duas características principais definem…
Trabalhe com nossa equipe para criar sua pilha ideal de software de cadeia de suprimentos e adaptá-la às suas necessidades comerciais exclusivas.