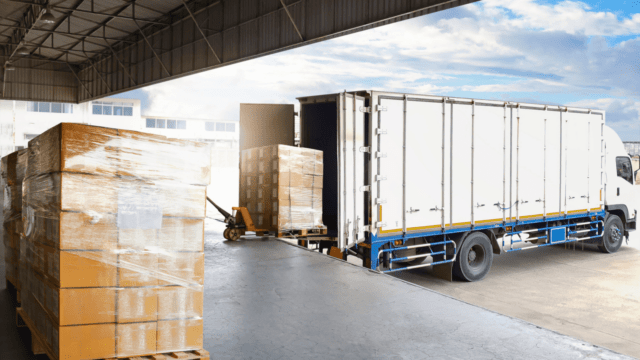
Quali sono i vantaggi di un TMS (Transport Management System)?
L’uso di un TMS (Transport Management System) consente di gestire tutte le operazioni di trasporto di un sito logistico. Dalla…
Medial International sceglie Generix WMS per digitalizzare le proprie operazioni logistiche Vai al comunicato stampa
La logica utilizzata durante la fase di stoccaggio si applica anche a quella della preparazione. All’interno dei magazzini o delle aree di deposito tradizionali, una pratica comune prevede la preparazione nella parte inferiore della scaffalatura dei pallet: le ubicazioni di riserva sono situate in alto con pallet completi, mentre quelle nella parte inferiore sono occupate da pallet da prelevare all’unità o al collo.
Per massimizzare la performance delle attività di preparazione, nel WMS (Warehouse Management System) sono fondamentali la correlazione tra la domanda e l’organizzazione e l’adattamento della gestione dei picking alle diverse tipologie di vendita.
Per questo, il software gestione magazzino proporrà di gestire le ubicazioni di preparazione dei picking in modo “statico” o “dinamico”. In ogni caso, queste modalità di gestione restano complementari tra loro e consentono di adeguare le attività alle esigenze del mercato. Ecco perché un picking “dinamico” può diventare “statico”, ad esempio quando la domanda associata al prodotto decresce nel corso dei giorni o delle stagioni.
Il picking statico – una pratica attualissima all’interno delle organizzazioni cosiddette lineari – è associato a un percorso di preparazione corrispondente alla logica di circolazione nelle corsie. Viene utilizzato con l’obiettivo di ottimizzare gli spostamenti, la costituzione dei supporti di preparazione oppure la sistemazione all’interno del contenitore o del collo.
Questa modalità permette in definitiva di evitare le rotture di carico a fine preparazione o all’arrivo presso il cliente. In altre parole, nei limiti del possibile si privilegia sin dall’inizio un ordine in un solo collo. Si evita quindi di dover imballare di nuovo gli articoli a fine preparazione o di spedirli in due colli quando ne sarebbe sufficiente uno soltanto.
La creazione dei circuiti di preparazione è definita dal responsabile degli stock in funzione delle esigenze dei clienti. Essa rispetta le regole legate ai prodotti: categoria, famiglia, peso/volume, rotazione ecc. Esiste tuttavia una molteplicità di combinazioni possibili che consentono di ottimizzarne la costituzione e favorirne la complementarietà. Gli algoritmi sono quindi importanti nel software WMS per dare al responsabile logistico visibilità sul binomio strategico carico/capacità.
Come ultima fase viene stabilito un percorso in base all’analisi dei dati relativi alla vita del magazzino, combinando lo spazio disponibile alla tipologia dei prodotti in funzione della domanda. Durante lo stoccaggio degli articoli in ricezione si utilizzeranno altri calcoli per proporre ubicazioni di riserva quanto più possibile vicine ai picking corrispondenti a ogni referenza.
Con il picking dinamico o “vincolato” si ricalcola l’esecuzione dei picking in maniera agile al momento dell’elaborazione dell’onda di preparazione in funzione dei vincoli inerenti:
Verranno quindi creati degli algoritmi per impostare dei picking corrispondenti a ogni referenza nella maniera più opportuna. Questo approccio si rivela molto efficace per gestire gruppi di referenze relativamente esigui, che sono soggetti a una domanda molto elevata durante un periodo limitato. Ad esempio, durante il lancio di una nuova collezione o di una promozione.
Il “batch picking” o “prelievo a lotti” è un metodo di preparazione degli ordini in cui avviene il prelievo simultaneo di più unità di uno stesso codice SKU per diversi ordini.
Nel concreto, il preparatore utilizza un carrello di preparazione sul quale dispone una serie di contenitori corrispondenti ad altrettanti ordini diversi. Potrà quindi distribuire la stessa referenza su più ordini nello stesso punto di prelievo, riducendo così al minimo i suoi spostamenti. Per agevolare il lavoro del preparatore, un algoritmo calcola la ripartizione delle missioni raggruppandole in maniera ottimale.
Questo principio è particolarmente utilizzato nei settori dell’e-commerce e del tessile che generano enormi quantità di piccoli ordini (di solito da 1 a 3 pezzi).
Si possono distinguere quattro grandi tipologie di missioni di un carrellista:
Queste attività possono essere combinate o incrociate. In questo caso si utilizza il termine inglese di interleaving.
Massimi livelli di produttività si possono raggiungere attraverso la combinazione delle missioni di stoccaggio con quelle di destoccaggio. Il più delle volte si combinano due missioni i cui punti di deposito e di prelievo massivo si trovano nella stessa corsia. Queste strategie sono particolarmente efficaci in quelle aree di stoccaggio definite “corsie strette” (VNA, very narrow aisle) dove i carrelli trilaterali (turret truck) sono più lenti. Sono anche fondamentali in caso di utilizzo di carrelli automatici (AGV, Automated Guided Vehicle), le cui velocità di spostamento sono particolarmente lente.
È altresì possibile determinare la costituzione delle missioni in funzione di un algoritmo di calcolo delle distanze. Questa funzionalità è implementata grazie alla parametrizzazione di un distanziatore, ossia uno strumento che consente di creare punti di riferimento e collegamenti tra le corsie di stoccaggio in modo da calcolare la lunghezza del tragitto tra due punti ubicati in corsie differenti.
La triangolazione è un metodo utilizzato per misurare gli spazi su scala umana. Consente di determinare una distanza calcolando la lunghezza di uno dei lati di un triangolo e misurandone due angoli grazie a delle identità trigonometriche. Il software WMS parte da questo presupposto per applicare la triangolazione alla gestione magazzino e ottimizzare gli spostamenti fornendo i percorsi più diretti possibili.
La triangolazione si è dimostrata ottimale nei contesti di radiofrequenza, dove una serie di scenari assicura per i carrellisti o i trasportatori la creazione automatica delle missioni attraverso tale metodo. In questo caso gli algoritmi del programma gestione magazzino WMS lavoreranno a partire da diversi elementi:
Il WMS è inoltre in grado di calcolare in maniera intelligente l’assegnazione delle baie in due momenti chiave:
In funzione del punto in cui è stoccata la massa critica di un arrivo, in modo da assegnare la baia di carico quanto più vicina al punto di stoccaggio target preferenziale.
Sarà possibile scegliere la baia di carico quanto più vicina al punto di prelievo massivo, ma si potrà anche utilizzare una funzionalità di assegnazione dinamica.
Attraverso questa modalità di funzionamento il WMS logistica sarà in grado di sincronizzare flussi di diversa natura (mono o multi-ordine ecc.), assegnando dinamicamente una baia di carico finale durante la fase di convalida dei supporti a fine preparazione. L’algoritmo terrà quindi conto dello stato di congestione delle baie a fronte dei criteri di coerenza (cliente, data di consegna, ordine).
Si utilizzano anche metodi basati su algoritmi che consentono di riempire al massimo i furgoni. Questo compito viene eseguito per lo più in collaborazione con il TMS.
Il cross-docking consiste nel ridistribuire dei supporti in ricezione direttamente verso una baia di spedizione senza passare da una fase di stoccaggio. Gli algoritmi del WMS possono essere efficaci in più contesti. Nel caso di magazzini con grande estensione in lunghezza che non sono concepiti come piattaforme di cross-docking, ad esempio, si privilegerà un’assegnazione intelligente delle baie di ricezione e/o di spedizione in modo da avvicinarle e ridurre al minimo le distanze di spostamento.
Se le referenze in ricezione sono anche in stock, il software gestione magazzino WMS può eseguire algoritmi più sofisticati che terranno conto di numerosi parametri. In altre parole, è possibile soddisfare un’esigenza “mentre l’onda è in corso” con un pallet ricevuto in una baia. Il sistema è inoltre autorizzato a essere utilizzato sulla baia al fine di evitare trasferimenti successivi (allo scopo di ridurre al minimo le “rotture di carico”). In questo caso si può decidere di non rispettare il principio FIFO (First In First Out) con il sistema che verifica il rispetto delle date di scadenza e dei contratti con data garantita.
L’uso di un TMS (Transport Management System) consente di gestire tutte le operazioni di trasporto di un sito logistico. Dalla…
Quando le operazioni logistiche crescono e/o diventano più complesse, un software WMS (Warehouse Management System) diventa essenziale. Si tratta di…
Molte aziende sono ora impegnate in un approccio eco-compatibile.. Stanno mettendo in atto strategie per rispettare gli standard ambientali e…
Collabora con il nostro team e costruisci il software ideale per la supply chain, adattandolo alle tue esigenze aziendali.