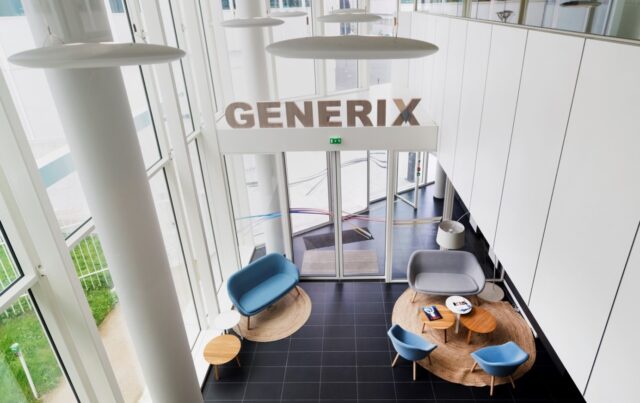
Generix renouvelle sa certification ISO 27001
Generix, éditeur de logiciels d’entreprise offrant un large portefeuille de solutions SaaS pour la chaîne logistique, la finance, le commerce…
Medial International choisit le système de gestion d’entrepôt (WMS) de Generix pour numériser ses opérations logistiques. Lire le communiqué
Transformez chaque connexion digitale en source de valeur
Vous souhaitez devenir un leader de l’économie en réseau ? Generix vous aide à piloter en toute confiance vos processus métiers digitaux les plus critiques dans les domaines de la supply chain, de la finance, de l’intégration B2B et du commerce.
Optimiser les trajets
+1M
opérations de transport par an
Rationaliser les échanges
+2B
messages EDI traités par an
Augmenter la productivité
+500M
factures électroniques traitées par an
Pilotez vos opérations critiques et collaborez au sein de votre réseau d’entreprise grâce à nos solutions SaaS à la pointe de la technologie, reposant sur des architectures modernes et respectant les derniers standards de sécurité. Tirez parti de vos données pour prendre les bonnes décisions et optimiser l’ensemble de vos ressources.
Gérez une supply chain durable et rentable et développez la collaboration à échelle mondiale.
Assurez une facturation fiable et automatisée de bout en bout, de l’achat au paiement.
Pilotez l’intégralité du parcours client omnicanal (B2C) pour une expérience fluide et sans couture.
Intégrez tous vos partenaires commerciaux à votre réseau d’entreprise et automatisez l’échange de données informatisé.
Bâtissez une supply chain résiliente, capable de gérer vos opérations de bout en bout, d’anticiper et de s’adapter aux évolutions du marché, tout en minimisant l’impact sur l’environnement.
Découvrez pourquoi plus de 2 000 entrepôts fonctionnent quotidiennement avec Generix WMS et SOLOCHAIN, reconnus pour leur flexibilité et leur richesse fonctionnelle.
Automatisez vos flux de données, vos transactions financières et vos processus de facturation pour réduire les opérations manuelles et garantir votre conformité réglementaire dans plus de 60 pays.
Explorez notre portefeuille complet de solutions et services SaaS dédié à la supply chain, la finance, le commerce et l’intégration B2B.
Generix, éditeur de logiciels d’entreprise offrant un large portefeuille de solutions SaaS pour la chaîne logistique, la finance, le commerce…
Turin, Italie, 5 mai 2025 – Generix, éditeur mondial de logiciels d’entreprise proposant une gamme complète de solutions SaaS pour…
Generix – éditeur de logiciels propose un portefeuille de solutions et de services cloud optimisés par l’IA pour piloter en…
Parlez-nous de vos challenges et préoccupations.