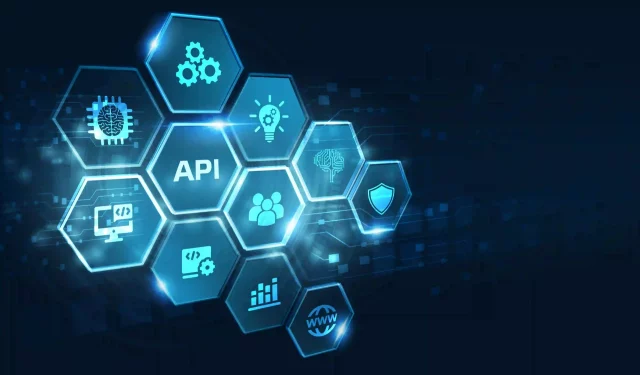
Standardisation de l’API PDP : un levier essentiel pour la conformité fiscale
L’API supportée par les Plateformes de Dématérialisation Partenaires (PDP) est un élément crucial pour la réussite de la réforme de…
Generix fournit des Schematrons universels pour améliorer l’interopérabilité de la facturation électronique entre les PDP Lire le communiqué
Assister l’opérateur avec un bras robotisé pour éviter les mouvements répétitifs des tâches d’assemblage ; améliorer les conditions de travail et réduire les risques ergonomiques lors des opérations de pick and place (déplacement de pièces ou de marchandises.) ; optimiser et sécuriser la palettisation… ce sont quelques-uns des avantages de la robotique collaborative dans le secteur logistique. Reste que, en pratique, cette collaboration entre un humain et un robot est loin d’être innée. Gros plan sur quatre bonnes pratiques.
Dans une approche CHR, l’humain et le robot ne se contentent pas de travailler côte à côte : ils s’exécutent ensemble, dans le même espace, avec un contact physique. La manière de définir et de répartir les tâches de chacun, en toute sécurité pour l’opérateur, est le premier grand challenge. Organiser et documenter l’allocation des tâches et sous-tâches de la collaboration hommes-robots est indispensable, mais pas suffisant. Pour garantir une collaboration durable et résiliente, de nombreuses variables et hypothèses doivent être prévues dès le départ pour laisser une certaine flexibilité au système et prévenir les risques. Par exemple, identifier les potentiels mouvements dangereux ou inefficients ; prendre en compte les facteurs cognitifs et psychologiques des collaborateurs (inattention, démotivation..), etc.
En 1996, Barbara J. Grosz, une grande chercheuse en informatique de Harvard, travaillait déjà sur les systèmes collaboratifs (source en anglais). Elle faisait alors remarquer que la collaboration entre un homme et une machine suppose à la fois une interaction entre les deux parties, c’est-à-dire une communication dans les deux sens, et également un partage d’intention. Ou autrement dit, la capacité à se comprendre mutuellement pour viser un objectif commun. Dans le secteur logistique, une bonne collaboration repose d’un côté sur la formation dispensée aux opérateurs pour la prise en main des outils digitaux et des interfaces hommes-machines. De l’autre, sur la capacité du robot à anticiper les comportements imprévus et intentions de l’humain, pour s’adapter en conséquence. Cela passe notamment par la prise en compte d’indicateurs objectifs, comme le temps ou la qualité. Équiper les opérateurs de capteurs sans fils est un autre moyen de nourrir le robot avec des données utiles, pour éviter les risques de collusion, par exemple. De nombreuses expérimentations basées sur la reconnaissance vocale sont en cours, permettant en outre aux robots de comprendre le langage naturel des opérateurs pour ajuster leurs actions.
La mise en place d’un système de collaboration hommes-robots suppose de remettre à plat l’organisation de l’entrepôt. Le risque serait donc d’imposer un recours aux cobots sans solide stratégie préalable. Le rôle d’un CRO, pour Chief Robotics Officer, consiste à jouer le chef d’orchestre au carrefour de l’ingénierie, des RH et du business. Il ne s’agit plus seulement de manager des collaborateurs, mais des équipes hybrides, composées d’humains et de robots. Ce profil est encore trop peu représenté. « De nombreuses organisations ne disposent pas de l’expertise interne en matière de robotique et d’automatisation (…) pour prendre des décisions éclairées et stratégiques », estime Dwight Klappich (anglais), VP analyste de Gartner Supply Chain.
96 % des professionnels du secteur logistique interrogés par Gartner utilisent ou envisagent d’utiliser l’automation cyber-physique dans les entrepôts ou les sites de production.1
Définition de système cyber-physique : c’est un ensemble d’outils informatiques qui collaborent pour contrôler des entités physiques, comme des cobots ou des exosquelettes…
Dans le contexte des entrepôts logistiques, une collaboration homme-robot efficace n’est pas fondée sur un duo mais bien sur un trio d’acteurs, tant le WMS joue lui aussi un rôle clé. En effet, les cobots doivent être capables d’échanger en temps réel avec le système global de gestion. Ainsi, la capacité du WMS à s’interfacer rapidement et facilement avec tous les outils et services d’automatisation sur lesquels sont branchés les robots est déterminante.
De plus, aussi intelligent soit-il, un robot n’est pas à l’abri d’une défaillance technique. Dans un modèle de CHR, les tâches allouées aux cobots doivent toujours être physiquement et techniquement accessibles aux opérateurs, de façon à ce qu’ils prennent le relais en cas de problème. Le cas échéant, le WMS doit lui aussi pouvoir basculer immédiatement en mode manuel pour éviter tout blocage de production.
Les solutions intégrées de gestion d’entrepôt de Generix répondent à ces enjeux clés d’interfaçage et de réversibilité. Elles facilitent en outre l’adoption (et l’acceptabilité) des robots par les équipes, grâce à des interfaces user-friendly dopées à la gamification.
1 Selon Gartner Supply Chain Practice, septembre 2021 (anglais)
Ces contenus pourraient également vous intéresser :
L’API supportée par les Plateformes de Dématérialisation Partenaires (PDP) est un élément crucial pour la réussite de la réforme de…
Dans un environnement logistique en constante évolution, une gestion agile et précise des ressources en entrepôt est essentielle pour rester…
Avec l’ouverture imminente du service annuaire et la publication des spécifications techniques axées sur les flux de déclaration, les cas…
Travaillez avec nos équipes pour concevoir et mettre en œuvre la Supply Chain qui accompagnera votre croissance, adaptée à vos spécificités métier.