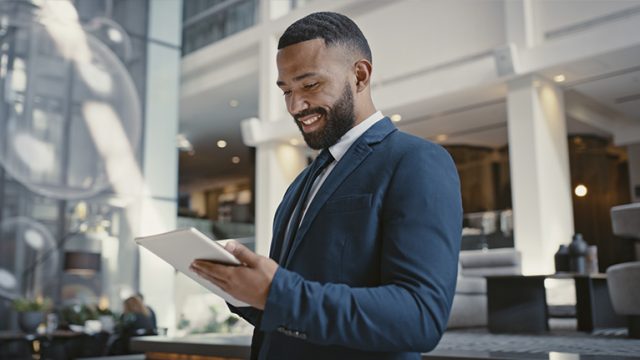
Three Months Before the B2B Mandate in Germany: Questions Arise About Reform Preparation
The B2B mandate in Germany, set to take effect on January 1, 2025, marks a crucial step in the European…
Medial International Chooses Generix Warehouse Management System (WMS) to Digitalize Its Logistics Operations Read the press release
Inspired by initiatives in South America, the reform is not limited to electronic invoicing. Tax authorities may eventually regulate other types of digital transactions, including:
The ultimate goal is to strengthen the fight against tax fraud using advanced tools such as fiscal datamining and artificial intelligence.
To gain PDP status, candidates must meet stringent requirements:
These requirements aim to foster the development of European cloud sovereignty and artificial intelligence alternatives.
This is not just a French initiative. Across Europe, similar movements are taking shape:
However, implementing these regulations remains complex:
For instance, some companies demand:
This reform highlights a strategic shift: reducing dependency on American software vendors and hyperscalers. Electronic invoicing serves as a pretext to strengthen French and European digital sovereignty.
Is this just the beginning of a broader independence movement? Only time will tell.
Streamline your invoicing processes across 65+ countries with our e-invoicing solution, fully compliant with regulatory and security requirements:
Discover our solution
The B2B mandate in Germany, set to take effect on January 1, 2025, marks a crucial step in the European…
Following the October 15 announcement regarding the abandonment of the PPF development, the DGFIP and its partner AIFE are ramping…
For several years now, e-commerce has been disrupting supply chains—and this trend is here to stay. In 2020, global online…
Work with our team to build your ideal supply chain software stack and tailor it to your unique business needs.