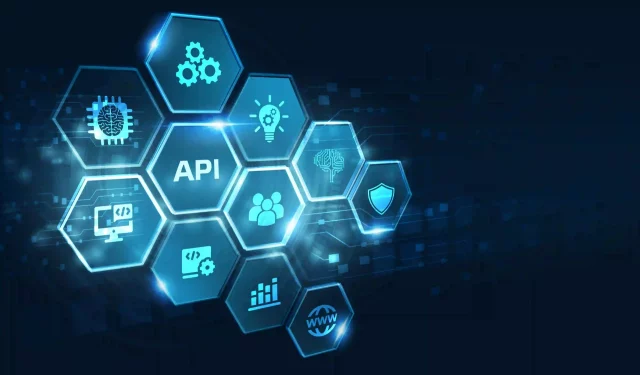
Standardisation de l’API PDP : un levier essentiel pour la conformité fiscale
L’API supportée par les Plateformes de Dématérialisation Partenaires (PDP) est un élément crucial pour la réussite de la réforme de…
Generix fournit des Schematrons universels pour améliorer l’interopérabilité de la facturation électronique entre les PDP Lire le communiqué
Le fonctionnement du WMS repose sur l’utilisation intensive d’algorithmes. Cependant, celle-ci est différente de ce qui est pratiqué avec l’intelligence artificielle, dont la démocratisation alimente le débat autour de la transparence et de l’explicabilité des calculs.
On pourrait distinguer l’utilisation classique des algorithmes par le mode opératoire, qui s’appuie sur une recherche multicritère qu’on pourrait qualifier de discriminante ou d’arborescente. On la dissocie de l’utilisation des outils IA qui permettent un calcul d’optimalité plus souple.
Avec l’équipe du Data Lab, Generix privilégie l’utilisation des outils d’IA pour les sujets très complexes avec un grand nombre de variables, ou bien lors d’analyses poussées de type Business Intelligence – statistiques de productivité, par exemple.
Couplés à des outils de visualisation puissants, ils facilitent l’analyse et la prise de décision – c’est notamment le cas avec notre Data Lab. Cependant, dans la plupart des cas traités par un WMS, le mode « classique » donne entière satisfaction.
À la suite de ces explications, nous pouvons désormais vous présenter le premier article d’une nouvelle série : l’occasion de faire un tour d’horizon de quelques fonctionnalités WMS mettant en jeu des calculs algorithmiques.
Dès leur réception, les produits, quels qu’ils soient, peuvent être rangés à de multiples endroits de l’entrepôt. On dispose généralement de plusieurs types de zones de rangement : racks pour palettes complètes de différentes dimensions et tolérances de poids, emplacements pour stockages de cartons, alvéoles pour stockage unitaire en vue d’un prélèvement… Le tout, en mode manuel ou mécanisé, et disponible en de multiples variantes.
Pour chacune des catégories ci-dessus présentes dans un entrepôt, il existe une répartition géographique des emplacements, dont l’accès est plus ou moins simple.
Lors du paramétrage du WMS, on peut attribuer à chaque emplacement des critères qui vont définir leur accessibilité, les types de préparation autorisés et leur inclusion dans des circuits de préparation. Conjointement, on va travailler sur une catégorisation des produits à partir des nombreuses caractéristiques disponibles dans le référentiel (données de base ou « Master Data ») : caractéristiques physiques, type de conditionnement, famille de produit, taux de rotation, etc.
Le rôle du WMS va être de traiter toutes ces informations pour calculer ensuite la meilleure façon de les ranger. Pour cela, on va utiliser une stratégie de rangement qui fait appel à un algorithme – c’est la stratégie de recherche d’emplacement (SRE).
Cet algorithme optimise la manière de stocker les produits en fonction de critères choisis parmi ceux cités précédemment. Un paramétrage permettra ensuite d’utiliser un critère plutôt qu’un autre, et d’en prioriser certains en fonction des objectifs.
In fine, l’optimisation consiste à stocker les produits à un endroit pratique en vue de la préparation de commande, l’opération la plus chronophage du process. Les produits à forte rotation seront donc placés le plus près possible des stations d’emballage, ou des quais d’expédition selon les cas.
Pour cela, on va bien souvent s’appuyer sur le taux de rotation des stocks (vitesse à laquelle un produit se renouvelle dans l’entrepôt ). On parle alors de « stratégie ABC » : A correspondant aux produits à forte rotation, et C à ceux qui prennent la poussière, également appelés « slow movers ». Le rangement peut se faire selon la classification ABC en priorité, puis se coupler avec d’autres critères selon le paramétrage choisi.
Le WMS offre également la possibilité de travailler avec un algorithme de saupoudrage, qui permet de répartir les produits dans différentes allées plutôt que de remplir une même zone avec une seule référence. On utilise cette stratégie lors d’un arrivage massif d’une référence destinée à être distribuée rapidement. Ceci permet d’éviter les embouteillages de caristes dans une même allée lors de la préparation !
Autre choix souvent utilisé : le stockage au plus près du picking. Dans le cas de prélèvement en bas de palettier, on paramétrera l’usage d’un algorithme qui stockera préférentiellement les palettes de réserve juste au-dessus, puis à côté des emplacements de prélèvement de cette même référence. À la clé : des missions de réapprovisionnement d’autant plus courtes.
L’API supportée par les Plateformes de Dématérialisation Partenaires (PDP) est un élément crucial pour la réussite de la réforme de…
Dans un environnement logistique en constante évolution, une gestion agile et précise des ressources en entrepôt est essentielle pour rester…
Avec l’ouverture imminente du service annuaire et la publication des spécifications techniques axées sur les flux de déclaration, les cas…
Travaillez avec nos équipes pour concevoir et mettre en œuvre la Supply Chain qui accompagnera votre croissance, adaptée à vos spécificités métier.