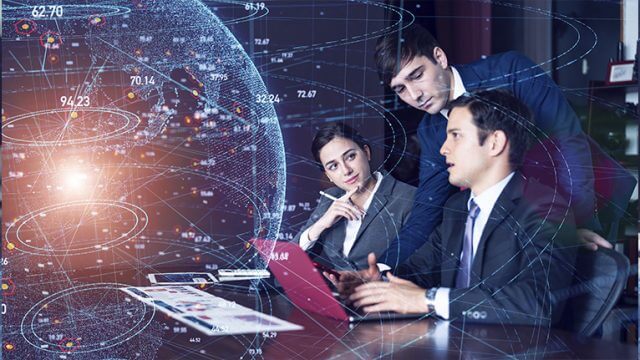
E-Invoicing and Its Geopolitical Stakes
France’s electronic invoicing reform relies on a Y-architecture, where Partner Dematerialization Providers (PDPs) play a central role in issuing and…
Generix Delivers Schematron for Electronic Invoicing to AFNOR to Ensure Interoperability Between PDPs Read the press release
Manufacturers found themselves facing several shocks simultaneously. Initially, massive jumps in demand confronted producers of consumer staples such as groceries and home supplies, purchased by consumers caught in a frenzy of panic buying. In addition, consumers largely turned away from in-person shopping in retail stores and moved their purchases online.
For example, Small Business Trends reports that online grocery shopping grew by a factor of seven times during the first wave of the pandemic. This growth in online shopping goes beyond just groceries. In fact, a recent survey found that 20% of those polled bought physical goods online for the first time during the pandemic.
As time wore on, demand composition changed. Consumers adjusted to working from home, spending their dollars on more comfortable clothes, new entertainment options and fitness equipment, and pursuits like baking sourdough bread. While the service economy continued to suffer, the producers of physical goods saw spikes in demand for their wares.
Reversing the Trend The last 20 years have been characterized by a move to JIT production and sourcing from low cost jurisdictions, such as China and Vietnam, which were among the first to lock down in the face of the pandemic. While this offshoring of production was historically beneficial for the bottom line, it left most organizations exposed to a systemic shock, precisely the kind of worst-case scenario brought about by the pandemic. The response to this has been renewed interest in ensuring supply chain resiliency.
According to IDC Manufacturing Insights, supply chain resiliency is “the capability of a manufacturing supply chain to ensure and preserve the continuity and consistency of product supply and meet business obligations for product delivery and service to customers by anticipating and being prepared for both short-term operational and long-term strategic disruptions.”
With economic activity—including manufacturing—now picking up and erasing many of the losses incurred early in the pandemic, the business world has settled into a new steady state characterized by intense and constant change. This “new normal” environment demands supply chains that rely not on JIT production and low-cost manufacturing, but rather on high levels of resiliency that allow them to ride out the highs and lows of whatever is thrown at them.
As they work to improve their supply chains’ resilience and evaluate where to make investments in tools, processes, and people, Bain & Co., tells manufacturers to factor in these five key tenets of supply chain resiliency:
For manufacturers, the first step to improving supply chain resiliency is to establish end-to-end visibility of the supply chain. That means mapping out all actors in the supply chain, across geographies and down to the tier 2 and tier 3 suppliers that characterize most supply chains with a strong Asian component.
According to McKinsey, since the pandemic hit, “39% of manufacturing organizations have implemented a nerve-center or control-tower, approach to increase end-to-end supply-chain transparency.”
This enhanced visibility is made possible through the deployment of technology. “Digital tools are making real-time visibility and traceability a reality, including a better understanding of potential failure points,” Bain & Co., points out. “Whatever new shocks the future may bring, organizations can now design supply chains to be more flexible and less vulnerable than ever before.”
These same digital tools can be deployed outside of the factory, McKinsey adds, “reaching across the end-to-end value chain to address planning (and replanning) challenges related to disruptions at suppliers or production plants, operational challenges in managing workplace health risks, and delivery challenges posed at transportation modes or in warehouses.”
Manufacturing execution systems (MES) help manufacturers achieve their supply chain resiliency goals. A solution that aligns with enterprise resource productivity platforms and warehouse management solutions, MES offers material visibility, automated task execution, and real-time traceability throughout the supply chain.
Armed with good visibility, manufacturers can diversify their supply chains away from vulnerable single source providers, and particularly those located in countries where the pandemic and other disruptions have been poorly managed.
With manufacturing experts agreeing that the “new normal” is here to stay, manufacturers are undertaking numerous initiatives to meet COVID-relate challenges. With many initiatives accomplished in record time, they’ve worked to achieve supply chain resiliency, laid the groundwork for reshoring production, undertaken new distribution strategies, and deployed new technology. Combined, these efforts will help manufacturers create future-proof supply chains that can weather any storm.
Generix Group North America provides a series of solutions within our Supply Chain Hub product suite to create efficiencies across an entire supply chain. Our solutions are in use around the world and our experience is second-to-none. We invite you to reach out to us here to learn more.
France’s electronic invoicing reform relies on a Y-architecture, where Partner Dematerialization Providers (PDPs) play a central role in issuing and…
The B2B mandate in Germany, set to take effect on January 1, 2025, marks a crucial step in the European…
Following the October 15 announcement regarding the abandonment of the PPF development, the DGFIP and its partner AIFE are ramping…
Work with our team to build your ideal supply chain software stack and tailor it to your unique business needs.