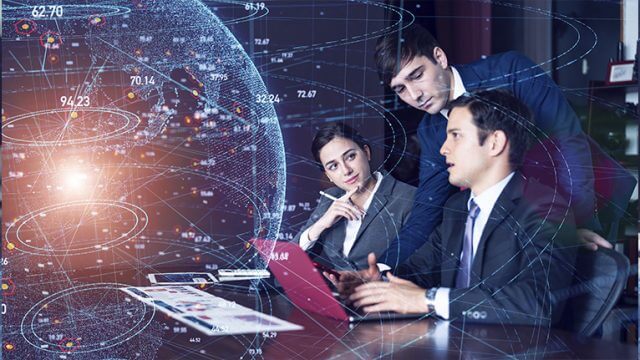
E-Invoicing and Its Geopolitical Stakes
France’s electronic invoicing reform relies on a Y-architecture, where Partner Dematerialization Providers (PDPs) play a central role in issuing and…
Medial International Chooses Generix Warehouse Management System (WMS) to Digitalize Its Logistics Operations Read the press release
WMS operation is based on the intensive use of algorithms. However, this is different from what is practiced with artificial intelligence, where popularity fuels the debate around calculation transparency and explainability.
We could distinguish the classical use of algorithms by the modus operandi, which is based on multi-criterion research that could be described as discriminatory or arborescent. It is separated from the use of AI tools that allow for more flexible optimal calculations.
With the Data Lab team, Generix favors the use of AI tools for very complex subjects with a large number of variables, or for in-depth analysis of Business Intelligence, such as productivity statistics, for example.
Coupled with powerful visualization tools, they facilitate analysis and decision making, as is the case with our Data Lab. However, in the majority of cases handled by a WMS, the “classic” method provides total satisfaction.
Following these explanations, we can now present the first article of a new series: an opportunity to take a look at some WMS features involving algorithmic calculations.
As soon as they are received, products of any kind can be stored in multiple locations within the warehouse. There are usually several types of storage zones: racks for full pallets of different size and weight capacities, slots for cardboard box storage, alveolus cells for unit storage prior to collection… Everything is offered as manual or mechanized options, and available in multiple variants.
For each of the above categories in a warehouse, there is a geographical distribution of locations, with varying ease of accessibility.
When setting up the WMS, each location can be assigned criteria that will define their accessibility, the types of preparations allowed and their inclusion in preparation circuits. Collectively, we will work on product categorization based on the many characteristics available in the repository (basic data or “Master Data”): physical characteristics, type of packaging, product family, turnover rate, etc.
The role of the WMS will be to process all this information and then calculate the best way to store it. To do so, we’ll use a storage strategy based on an algorithm – This is the Site Reliability Engineering (SRE).
This algorithm optimizes the way products are stored based on criteria chosen among those mentioned above. A setting will then allow one criterion to be used over another, and to prioritize certain ones depending on the desired end goal.
Ultimately, optimization consists of storing products in a convenient location for order preparation, the most time-consuming operation of the process. High-rotation products will therefore be placed as close as possible to packing stations, or shipping docks, depending on the case.
This will often be done by relying on the rate of stock turnover (the speed at which a product is renewed in the warehouse). This is known as an “ABC strategy“: “A” refers to high-rotation products, and “C” to dust-taking products, also known as “slow movers”. Storage can be done according to the ABC classification as a priority, and then pair with other criteria depending on the setting chosen.
The WMS also offers the possibility of working with a scattering algorithm, which allows products to be distributed across different aisles rather than filling one zone completely with a single item. This strategy is used when an item arrives in mass and is destined for quick distribution.
This helps avoid heavy traffic amongst forklift operators in a given aisle during preparation!
Another commonly used choice: storage close to “picking.” When sampling a pallet from a bottom level, an algorithm is used to preferentially store reserve pallets just above it and next to the sampling locations of the same item. The key is: even shorter resupply missions.
France’s electronic invoicing reform relies on a Y-architecture, where Partner Dematerialization Providers (PDPs) play a central role in issuing and…
The B2B mandate in Germany, set to take effect on January 1, 2025, marks a crucial step in the European…
Following the October 15 announcement regarding the abandonment of the PPF development, the DGFIP and its partner AIFE are ramping…
Work with our team to build your ideal supply chain software stack and tailor it to your unique business needs.