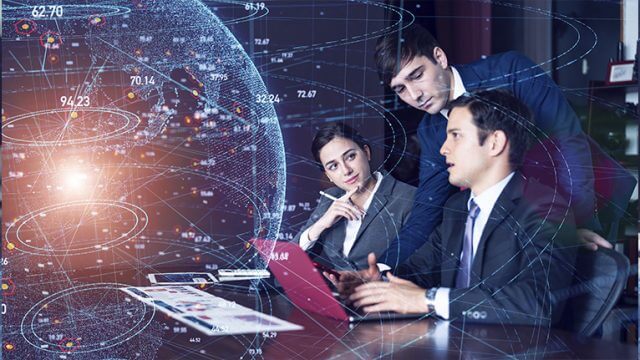
E-Invoicing and Its Geopolitical Stakes
France’s electronic invoicing reform relies on a Y-architecture, where Partner Dematerialization Providers (PDPs) play a central role in issuing and…
Generix Delivers Schematron for Electronic Invoicing to AFNOR to Ensure Interoperability Between PDPs Read the press release
In the WMS market, the majority of U.S. companies are using a solution today. However, according to a Generix Group study, 42% of companies felt that their current WMS solution was increasingly less tailored to their needs. Changes in warehouse activities have pushed the need to replace outdated systems with ones that allow for adaptations, agility, and advanced capabilities.
For growth-oriented businesses having a WMS is a strategic move that will support building a new-generation warehouse. New modes of consumption, changing buyer behaviors, and high customer expectations mean warehouses need to be faster, more productive, error-free, and forward-looking.
The newest generation of WMS solutions have expanded to adapt to these changes creating a competitive environment for warehouses. An advanced WMS will help your warehouse or distribution center:
Despite the digitization of warehouses that started in the 1980s, paper continues to be used by some in conjunction with scan verification technologies, automation systems, and warehouse management solutions like WMS or ERP modules.
While paper-based processes may be appropriate for a smaller operation with fewer operational requirements, reliance on paper will limit business expansion, whether through increasing volume, taking on new fulfillment channels, or moving from a single channel fulfillment to a multi-channel, cross-channel, or even omni-channel.
Three common paper-based processes still used warehouse operations: manual data entry, manual printing and sorting of pick tickets, and added verification steps for accuracy.
In logistics, there is little tolerance for error. As a result, customer satisfaction depends on warehouse performance. A WMS can eliminate the workaround of these paper-based processes and boost productivity, ensuring that item locations are accurate, pick lists and routes are clear-cut, control is enhanced, the warehouse layout is optimized, processes are standardized and continuously enriched, and business data is visible and actionable.
If your company is looking to optimize your warehouse operations and wants to learn more about how an advanced WMS can support that business objective, download our Absolute Guide WMS.
Generix Group North America provides a series of solutions within our Supply Chain Hub product suite to create efficiencies across an entire supply chain. Our solutions are in use around the world and our experience is second-to-none. We invite you to contact us to learn more.
France’s electronic invoicing reform relies on a Y-architecture, where Partner Dematerialization Providers (PDPs) play a central role in issuing and…
The B2B mandate in Germany, set to take effect on January 1, 2025, marks a crucial step in the European…
Following the October 15 announcement regarding the abandonment of the PPF development, the DGFIP and its partner AIFE are ramping…
Work with our team to build your ideal supply chain software stack and tailor it to your unique business needs.