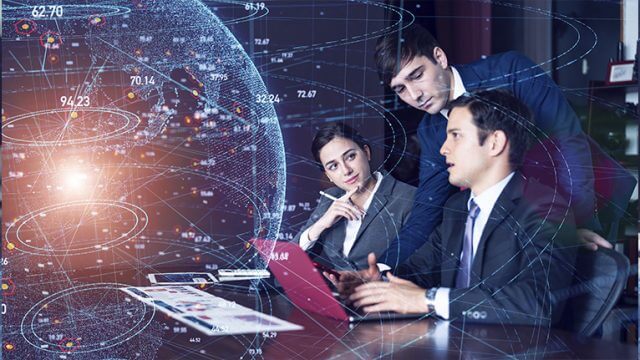
E-Invoicing and Its Geopolitical Stakes
France’s electronic invoicing reform relies on a Y-architecture, where Partner Dematerialization Providers (PDPs) play a central role in issuing and…
Medial International Chooses Generix Warehouse Management System (WMS) to Digitalize Its Logistics Operations Read the press release
Locus Robotics provides mobile robots deployed in logistics centers and warehouses to handle order picking and inventory replenishment. Designed primarily for the retail, e-commerce and pharmaceutical industries, this agile solution replaces manual picking carts with automated ones. “The particularity of our solution is that we deploy a collaborative multi-bot solution, which works in harmony with humans,” notes Denis Niezgoda, VP Europe of Locus Robotics, “the automats navigate between the different zones, guided by artificial intelligence, while the employees remain in their aisles This innovative organization absorbs about 50% of the operators’ movements“. This makes manual work less tedious and much more efficient. “Perfect for meeting the needs of agile logistics, which requires accelerated order preparation and multi-customer preparation“, confirms Isabelle Badoc, Product Marketing Manager at Generix.
To go further on the theme of productivity in warehouses, also discover this dedicated content: First mile management: gain in reactivity after the order!
Born in Boston in 2010, Locus Robotics has already invested in a hundred sites worldwide and has been accelerating its development in Europe for a few months, in particular thanks to its strategic partnership with Generix. With nearly 450 million items collected so far, Locus’ robots are not idle! It’s normal for the automation solution to double or triple the productivity of the warehouse in which it is deployed, especially in picking, to meet the many challenges of the supply chain. The other advantage of Locus? Scalability. Deployable in a maximum of 4 weeks, on a subscription model, the Locus fleet does not require heavy investments and can be adapted to any type of warehouse. “As our service is easily deployable, it becomes easier for our customers to absorb peaks of activity, for example during Black Friday or Christmas: it is enough to add more robots in the yard“, says Denis Niezgoda.
But automatons don’t do everything. To be fully operational, they must perform their tasks in total harmony with their flesh-and-blood colleagues. As we have seen, an artificial intelligence guidance system allows them to navigate the aisles autonomously, avoiding collisions with their fellow human operators. To facilitate their adoption, an intuitive interface, based on gamification, allows operators to take control immediately.
The service must also be integrated into the warehouse management system. “We enter the capacity and velocity data from the automats to integrate them into the overall resource planning and mission allocation,” explains Isabelle Badoc of Generix, whose WMS can be easily interfaced with automation services such as those offered by Locus. “We will thus be able to assign the right automation resources to the right operators, and above all, to define the processes at the output of mechanized systems to avoid bottlenecks“.
This integrated management also allows total reversibility because robots, after all, are not infallible. “In the event of a breakdown or slowdown, it is necessary to be able to switch from automated order preparation to manual picking in almost real time, and interfacing with the WMS makes this possible,” says Isabelle Badoc, who shows that the automated warehouse must be designed as a complete and interdependent ecosystem.
If the deployment of automatic carts will probably accelerate in the next few years, the unexploited possibilities of warehouse robotization are still numerous: “Vertical movements can still be optimized (in non-equipped warehouses), as well as packaging or physical transfer in the carts represent the future,” says Denis Niezgoda. “In an industry that is still very manual, you will see an increase in automation in the coming years!” says Isabelle Badoc.
France’s electronic invoicing reform relies on a Y-architecture, where Partner Dematerialization Providers (PDPs) play a central role in issuing and…
The B2B mandate in Germany, set to take effect on January 1, 2025, marks a crucial step in the European…
Following the October 15 announcement regarding the abandonment of the PPF development, the DGFIP and its partner AIFE are ramping…
Work with our team to build your ideal supply chain software stack and tailor it to your unique business needs.