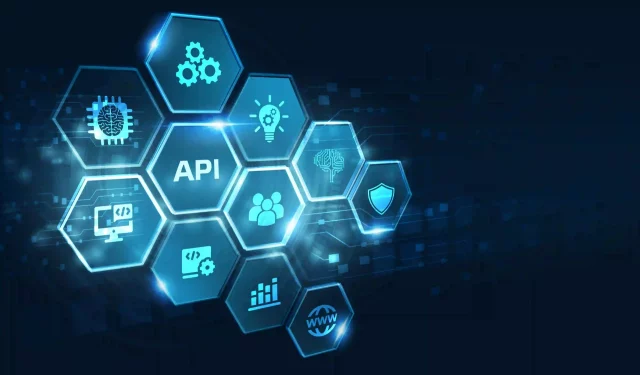
Standardisation de l’API PDP : un levier essentiel pour la conformité fiscale
L’API supportée par les Plateformes de Dématérialisation Partenaires (PDP) est un élément crucial pour la réussite de la réforme de…
Generix fournit des Schematrons universels pour améliorer l’interopérabilité de la facturation électronique entre les PDP Lire le communiqué
Basée sur les découvertes de Thales et le théorème de Pythagore, la triangulation est une méthode mathématique utilisée pour calculer des distances. Le principe consiste à mesurer les angles d’un triangle dont on connaît certaines dimensions pour en déduire des distances.
En entrepôt, la triangulation est mise à profit pour optimiser les distances à vide en proposant aux caristes les missions les plus proches, à priorité égale. Ce procédé peut être appliqué aux tâches de stockage et déstockage, d’approvisionnement par picking, de transfert et de préparation de commandes par box.
La triangulation en entrepôt permet d’adapter les priorités en temps réel en fonction de la distance. Ainsi, une mission peu urgente peut passer en priorité si elle nécessite un déplacement moins important.
En matière de déstockage, les missions deviennent logiquement de plus en plus urgentes selon l’heure de chargement au plus tard. La triangulation est utilisée dans ce cas pour faire évoluer dynamiquement les priorités fixées pour chaque mission.
Prenons l’exemple de deux palettes à expédier respectivement dans 15 et 20 minutes. Si la palette qui doit partir dans 20 minutes correspond aux missions les plus proches géographiquement, elle sera traitée prioritairement.
À lire également : Comment favoriser la mobilité en entrepôt ?
Jonglant entre gestion des urgences et optimisation des opérations, les chefs d’entrepôt doivent aujourd’hui s’affranchir des critères de priorité pour optimiser les déplacements des caristes. Grâce à la fonction de triangulation du WMS Generix Group, ils disposent d’un outil permettant de limiter les trajets des opérateurs à priorité égale et de gérer les urgences de manière optimale. Un réel atout pour les chefs d’équipe en matière de gestion des ressources et des vagues de préparation. Envie d’en savoir plus sur la nouvelle version du WMS Generix Group ? Téléchargez la fiche produit !
L’API supportée par les Plateformes de Dématérialisation Partenaires (PDP) est un élément crucial pour la réussite de la réforme de…
Dans un environnement logistique en constante évolution, une gestion agile et précise des ressources en entrepôt est essentielle pour rester…
Avec l’ouverture imminente du service annuaire et la publication des spécifications techniques axées sur les flux de déclaration, les cas…
Travaillez avec nos équipes pour concevoir et mettre en œuvre la Supply Chain qui accompagnera votre croissance, adaptée à vos spécificités métier.