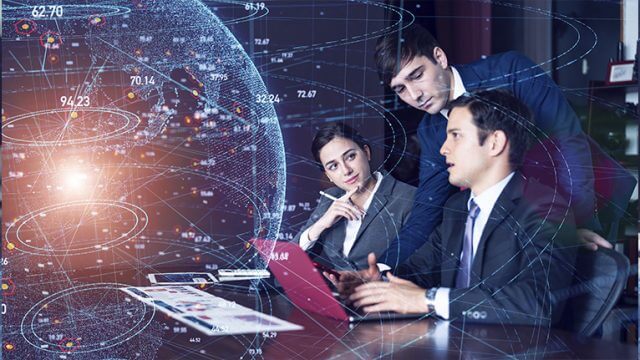
E-Invoicing and Its Geopolitical Stakes
France’s electronic invoicing reform relies on a Y-architecture, where Partner Dematerialization Providers (PDPs) play a central role in issuing and…
Generix chooses Kyndryl to modernize IT infrastructure Read the press release
Taking aim at the world’s manufacturing supply chains, COVID enacted a particularly steep toll on those global networks. Few sectors were spared, with the World Economic Forum anticipating “severe implications for international production networks” and a possibility that those impacts will span years.
“It happened faster than anyone could imagine,” Bain & Co., points out. “As China sent workers home and shuttered businesses in January to contain the coronavirus outbreak, the steady flow of vital parts to global supply chains slowed or stopped. The unexpected disruption sent shock waves through boardrooms around the world, just as the COVID-19 pandemic began to spread.” A Scaffolding for Long-Term Business Resiliency As manufacturers work to mitigate the current impacts of the pandemic while also fortifying their supply chains for the future, many of them are focusing on “resiliency” as a core value. Defined by McKinsey & Co., as, “equipping organizations to react more flexibly and efficiently to events that are beyond their influence by decoupling location and business outcomes,” resiliency incorporates people, processes, partners, and technology.
Achieving resiliency requires a combination of speed and discipline; a focus on creating transparency across multi-tier supply chains; and accurate inventory visibility along the entire value chain. To improve resiliency, companies also have to be able to assess realistic final-customer demand; optimize production and distribution capacity while also ensuring employee safety; identify and secure logistics capacity; and effectively manage both cash and net working capital.
Combined, these forces can drive transformative changes that would otherwise take years to plan and put into effect. Accelerated by COVID’s massive impacts on the supply chain, these changes are now taking place within mere months, providing the scaffolding for long-term business resiliency.
Here are six ways manufacturers can begin infusing more resilience into their global supply chains:
A recent Gartner survey found that just 21% of companies have what they consider to be “highly resilient networks,” which the firm defines as having good visibility and the agility to shift sourcing, manufacturing, and distribution activities around fairly rapidly. The rest of the companies don’t plan to sit around and wait for another disruption to strike.
“Increasing resilience will be a priority for many as they emerge from the current crisis,” Gartner points out. “with more than half of the companies surveyed expecting to be highly resilient within two to three years.”
France’s electronic invoicing reform relies on a Y-architecture, where Partner Dematerialization Providers (PDPs) play a central role in issuing and…
The B2B mandate in Germany, set to take effect on January 1, 2025, marks a crucial step in the European…
Following the October 15 announcement regarding the abandonment of the PPF development, the DGFIP and its partner AIFE are ramping…
Work with our team to build your ideal supply chain software stack and tailor it to your unique business needs.