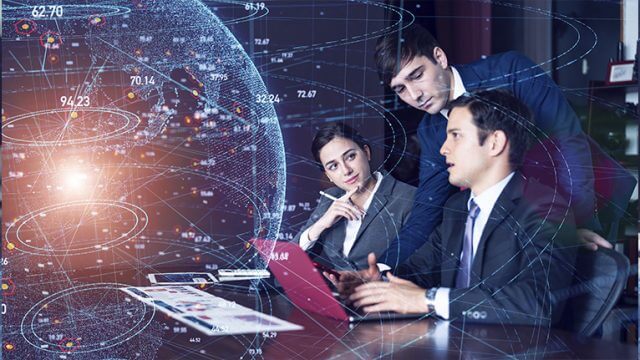
E-Invoicing and Its Geopolitical Stakes
France’s electronic invoicing reform relies on a Y-architecture, where Partner Dematerialization Providers (PDPs) play a central role in issuing and…
Generix Delivers Schematron for Electronic Invoicing to AFNOR to Ensure Interoperability Between PDPs Read the press release
The founders of Chapman’s Ice Cream started their company in 1973 with a shrewd decision. They chose to make a product that millions of Canadians love. But delighting ice cream lovers is one thing. Serving businesses that sell ice cream is quite another.
NOTE:
Consumers and commercial customers want different things from an ice cream brand. Distributors and retailers want services from an ice cream brand that consumers don’t even think about. Among other things, they want to receive their orders complete, on time, and without errors. They want accurate invoices. And they want shipments that are easy to unload and put away in stock.
Chapman’s delivers flavor, variety, quality… and solid logistics support
Today, Chapman’s prominence in Canada suggests they do a consistently good job of pleasing both types of customers. The award-winning, family-run company is the biggest independent ice cream maker in Canada.
Even with all their success, Chapman’s continued looking for ways to improve their business.
John Fleming, director of information technology, says the Chapman family sets a high bar for the company’s performance. “They operate on the principle that: If better is possible, then good isn’t good enough,” he says. This mindset led company executives to explore better ways to manage inventory several years ago.
The company was running a manufacturing-focused enterprise resource planning (ERP) system. Chapman’s executives liked their ERP system, but they wanted more inventory management capabilities. Chapman’s inventory processes were mostly manual, a hybrid of paperwork and spreadsheets. The company didn’t use barcodes. Consequently, it was hard to maintain real-time counts for both work in progress and finished goods.
The company also faced other challenges resulting from incomplete control over inventory: Inventory counts were inaccurate. Ingredients and finished goods moved through manufacturing and warehousing processes without updating inventory status. The tracking of inventory waste and shrink was manual and inaccurate. The result was often an unexpected year-end adjustment to inventory values. Their material-handling processes were manual and inefficient. They had inadequate control over the flow and tracking of ingredients and products through production and shipping.
Company executives decided to improve inventory management throughout their internal processes. They wanted the new system to address material handling, warehousing, production, and fulfillment. They also wanted a system that would integrate with their enterprise resource planning (ERP) system.
Those requirements led Chapman’s to choose the warehouse management system (WMS) from Generix Group North America.
After installing the WMS, Chapman’s had the inventory management they were looking for. “Every time someone touches the stock,” Fleming says, “they scan the barcode. The system moves inventory from the place where it was and then scans it into a new location.” “Now we know in real time where everything is. We can query that in the WMS, which is now our primary inventory management tool.”
Company gains real-time view of inventory, plus stock history and traceability
“If I want to know where the inventory is now,” Fleming says, “I can look at the chronology in the WMS. It gives me the history. I can see where it came from and the original lot on the original material instance. I can see what’s been used. I can also see the history of that material instance for that product in real-time. That’s been amazing for us.”
In addition, executives were pleasantly surprised that the new WMS delivered many benefits beyond inventory management. They also achieved these results:
Inventory is the lifeblood of most manufacturing and distribution businesses. It affects nearly every aspect of its operations. And it’s often one of a company’s biggest investments and most valuable assets.
With accurate controls and effective supply chain execution, smart companies use their inventory to delight their customers.
NOTE :
Dig deeper
For insights about the challenges of the food industry and how Generix Group can help, please go here.
France’s electronic invoicing reform relies on a Y-architecture, where Partner Dematerialization Providers (PDPs) play a central role in issuing and…
The B2B mandate in Germany, set to take effect on January 1, 2025, marks a crucial step in the European…
Following the October 15 announcement regarding the abandonment of the PPF development, the DGFIP and its partner AIFE are ramping…
Work with our team to build your ideal supply chain software stack and tailor it to your unique business needs.