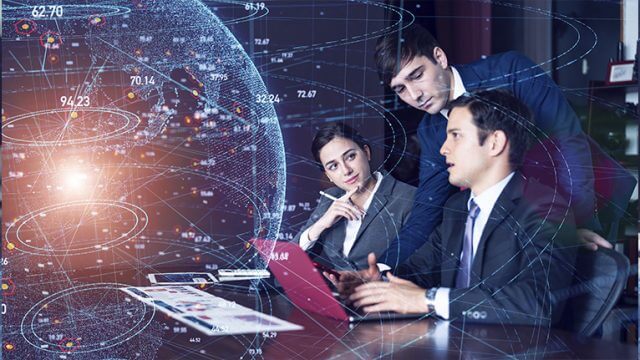
E-Invoicing and Its Geopolitical Stakes
France’s electronic invoicing reform relies on a Y-architecture, where Partner Dematerialization Providers (PDPs) play a central role in issuing and…
Generix Delivers Schematron for Electronic Invoicing to AFNOR to Ensure Interoperability Between PDPs Read the press release
It wasn’t long ago that the large material handling shows, Modex and ProMat, featured small robotics displays in their own section of the exhibition floor. Programmed to pick up boxes of Tic Tacs or ping pong balls and neatly arrange them in shipping boxes, robotic arms whirred and snapped as interested onlookers watched in amazement.
Fast-forward to 2020, and robotics technology can be seen—in some form or fashion—in nearly every booth on the floor of these huge industry trade gatherings. From autonomous robots that maneuver the floor alongside humans to robotic arms that have human-like sensory perception to intelligent applications that support the time-consuming product return process, robots and automation have a firm footing in today’s fulfillment centers.
COVID accelerated this trend. Not only did it drive more people to start shopping online—a trend that drove up e-commerce order volumes—but social distancing rules were put in place. As a result, the limited number of workers that can be on the floor at any given time and the need to “do more with less” in a recessionary period are pushing more companies to explore automation and robotics.
Social distancing at work means 1) fewer workers on the floor and 2) less productivity unless, of course, companies get up to speed on the automatics/robotics trend that was already in full force before COVID. Now, the technology that was already under development and/or in use is proving itself as a lifesaver in this new environment, where social workplace distancing and other regulations prevent companies from cramming hundreds of workers into small spaces.
Of course, automation has been around for a long time, with linear conveyor and sortation systems in use in the world’s warehouses for decades. With the introduction of automated guided vehicles (AGVs) and autonomous mobile robots (AMRs), more companies began to see “co-picking” of products as a way to reduce their reliance on labor. Letting robots handle repetitive tasks also improves the ergonomic environment and allows employees to focus on more important tasks.
“AGVs have been moving things around on behalf of humans for over half a century,” Fetch Robotics points out. “They’ve become a familiar fixture in factories, warehouses, and anywhere there’s a need for repetitive material delivery.”
The day when a control tower serves as the foundation for a fully-robotic fulfillment center that doesn’t rely on human labor (or even lights), isn’t far off. In fact, we’re already seeing this trend in the manufacturing space, where robotics has taken over a significant chunk of the physical labor. This enables higher levels of predictability and consistency from an output and manufacturing perspective, and helps companies better respond to their customers’ demands.
The dark warehouse isn’t a new concept, but it’s one that companies are examining more closely as a result of the global pandemic. They’re also paying more attention to the general use of robotics and automation in a busy setting where staying a full six feet away from the next person isn’t always feasible. The convergence of robots and automation in this setting can help companies—both in the COVID and post-COVID environment—keep their valuable human labor safe and healthy without the need to hire more help.
To achieve these goals, companies are exploring goods-to-person picking technology, high-density shuttles, and automated storage and retrieval systems (AS/RS), the latter of which facilitates higher storage density and greater cube utilization. By allowing warehouses to go “up” versus “out,” these technologies enable a smaller footprint and create new efficiencies for fulfillment operations.
At a more basic level, carousels can also help companies comply with new social distancing requirements. For example, a goods-to-person arrangement can be set up with plexiglass separators between work stations, thus minimizing close interaction between personnel. This adds another layer of protection: by allowing a separation of “man and machine” within the delivery mechanisms, the chance of a machine-related injury is significantly reduced.
Amazon is one company that’s been on the leading edge of the robotics-in-the-warehouse movement since it acquired Kiva Systems back in 2012. Now, the e-tailer is going a step further and looking to artificial intelligence (AI) as the answer to its social distancing challenges. According to Engadget, Amazon’s “Distance Assistant” helps its fulfillment facility employees keep a safe distance from one another.
Amazon has deployed the technology in a handful of its facilities, with plans to roll out more in the coming weeks. Using a time-of-flight sensor similar to the depth-sensing cameras found on smartphones like the Galaxy S20, the assistant measures the distance between employees. “The AI component is there to help it differentiate people from the background,” Engadget reports. “What the AI sees is then displayed on a 50-inch screen for workers to glance at as they pass high-traffic areas.”
The push to automate that started pre-COVID was largely driven by labor market constraints, plus the need for more predictability and less variability from a labor perspective. A work setting that’s known for its high employee turnover, the cost of training and retaining workers can take a bite out of the operator’s bottom line. Automation and robotics were already starting to “fill in” some of these gaps, and we expect that trend to continue over the next few years as companies recover from the impacts of COVID and prepare for the next potential disruption.
France’s electronic invoicing reform relies on a Y-architecture, where Partner Dematerialization Providers (PDPs) play a central role in issuing and…
The B2B mandate in Germany, set to take effect on January 1, 2025, marks a crucial step in the European…
Following the October 15 announcement regarding the abandonment of the PPF development, the DGFIP and its partner AIFE are ramping…
Work with our team to build your ideal supply chain software stack and tailor it to your unique business needs.