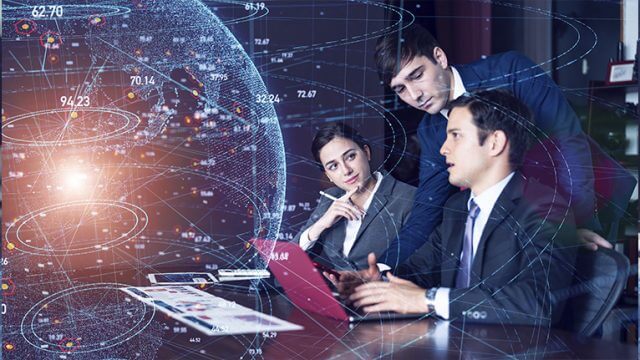
E-Invoicing and Its Geopolitical Stakes
France’s electronic invoicing reform relies on a Y-architecture, where Partner Dematerialization Providers (PDPs) play a central role in issuing and…
Generix Delivers Schematron for Electronic Invoicing to AFNOR to Ensure Interoperability Between PDPs Read the press release
In any given industry, it’s the companies that can leverage accurate data quickly and efficiently that have the power to achieve the levels of operational agility needed to gain a serious competitive advantage.
Operational agility is a key determinant of an operation’s efficiency and resiliency and is fundamental to a supply chain’s capacity to meet demand and achieve growth. In the Food & Beverage industry, the importance of operational agility was maybe never more obvious than at the peak of the Covid crisis. As supply chain disruptions became the norm, grocers who relied on technology solutions that provided them accurate data across the entire supply chain were able to quickly adapt their operation and processes to the changing conditions. The most agile were able to quickly open new sales and weather supply shortages, allowing them to maintain high levels of service and grow their share of the market.
Today, as the crisis subsides, these Food and Beverage companies find themselves in an advantageous situation. As the frequency and gravity of supply chain disruptions lessen, operators will regain the ability to look to future and to develop roadmaps for investments in their infrastructure and technology architecture. As they do, they will do well to keep in mind the lessons learned during the last few years and to continue to seek out the means towards greater operational agility.
In the age of integrated supply chains and multichannel operations, Food & Beverage companies are finding more and more that they can no longer rely on clerical processes or a simple ERP system to adequately support their activities. Technology solutions such as a WMS, MES, or TMS have become indispensable to companies looking to achieve and maintain the kind of operational agility that leads to greater efficiency, customer satisfaction, and sustainable growth. Not only do these solutions enable granular visibility on the data that really matters to them in real time, but they also make it possible to automate workflows and processes to achieve greater productivity and better margins.
A system like the SOLOCHAIN WMS, for instance, is known to provide that much needed and highly detailed information over inventory, workflows, and manufacturing processes across the entire supply chain, from vendors to clients. More importantly, SOLOCHAIN makes that data available in real time to workers on the floor as well as to management, empowering everyone to adapt to the updated information quickly and efficiently.
At a candy bar processing facility, for example, the SOLOCHAIN WMS supports warehouse workers across the entire manufacturing execution process. Workers overseeing the production of candy bars can see, for instance, when inventoried quantities for a given ingredient are running low. In such a case, SOLOCHAIN’s recipe management capabilities enable the WMS to suggest valid substitutions for missing ingredients. As soon as a new ingredient is selected, the changes are immediately communicated to workers affected to picking activities, ensuring that the right ingredients are picked for consumption henceforth and that production continues to run smoothly.
The SOLOCHAIN WMS can also optimize the candy bar maker’s operational agility through the automation of workflows in the warehouse. Once integrated with the company’s ERP system, SOLOCHAIN can be configured to automize the generation of POs when quantities for a given SKU reach a predetermined threshold. Thanks to such back-office functionalities and automated exchanges between the WMS and the manufacturer’s ERP system, inventory management and replenishment activities are much more efficient.
Yet another way the SOLOCHAIN WMS contributes to a company’s operational agility is by enabling operators to react quickly and with precision in the event of a recall. When poorly managed, recalls occasion costly and labor-intensive operations, which ultimately affects margins and an operator’s capacity to use their capital to better ends. Clumsy recalls can also negatively impact the trust customers put in the company, which severely hinders a its capacity to maintain its share of the market.
Operational agility is also improved at the candy bar maker thanks to SOLOCHAIN’s track and trace capabilities, which enable accurate and precise recalls. The WMS affords operators control and visibility over finished products through complete lot traceability. It allows them to identify if an item was consumed as an ingredient in a batch and trace that item through its entire journey, from vendor to final customer. Once an item is flagged as problematic, the system immediately initiates an electronic recall, informing all the relevant people and stakeholders of the batches location that need to be recalled and of the necessary actions to take.
Recipe management, dynamically updated inventory changes, automated data exchanges between the WMS and the ERP system, and precise traceability capabilities are just some of the ways in which the SOLOCHAIN WMS optimizes a Food & Beverage company’s operational agility. With increased agility, supply chain operators in the industry are in a better position to meet demand and explore new channels when the opportunity presents itself, giving them the upper hand against the competition.
Generix Group North America provides a series of solutions within our Supply Chain Hub product suite to create efficiencies across an entire supply chain. Our solutions are in use around the world and our experience is second-to-none.
To discover the advantages of the SOLOCHAIN WMS, take a look at the Product Sheet: https://info.generixgroup.com/US-WMS_SOLOCHAIN_Product_Sheet.html.
Generix Group North America provides a series of solutions within our Supply Chain Hub product suite to create efficiencies across an entire supply chain. Our solutions are in use around the world and our experience is second-to-none. We invite you to contact us to learn more.
France’s electronic invoicing reform relies on a Y-architecture, where Partner Dematerialization Providers (PDPs) play a central role in issuing and…
The B2B mandate in Germany, set to take effect on January 1, 2025, marks a crucial step in the European…
Following the October 15 announcement regarding the abandonment of the PPF development, the DGFIP and its partner AIFE are ramping…
Work with our team to build your ideal supply chain software stack and tailor it to your unique business needs.