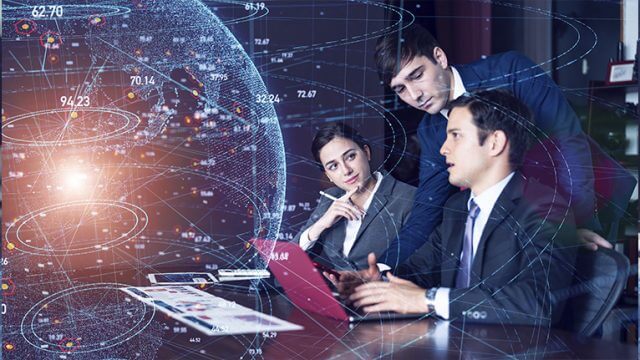
E-Invoicing and Its Geopolitical Stakes
France’s electronic invoicing reform relies on a Y-architecture, where Partner Dematerialization Providers (PDPs) play a central role in issuing and…
Generix Delivers Schematron for Electronic Invoicing to AFNOR to Ensure Interoperability Between PDPs Read the press release
To optimally manage scheduling and daily task assignments, warehouse managers require a detailed view of all available resources: human operators, robots, mechanized chains, sorters, equipment (carts, forklifts, etc.), and facilities (docks, racks, ventilation systems, etc.). Isabelle Badoc, Product Marketing Director at Generix, comments on the current scenario: “Managers are constantly juggling resource allocation to tasks to achieve the level of productivity required to meet volume objectives.” The rise of e-commerce has exponentially amplified this requirement, leading to increased processing volumes and a broader array of tasks. Concurrently, the associated flows are inconsistent and difficult to predict. As a result, the capacity to anticipate has become a crucial weapon in overcoming these challenges.
The e-commerce landscape necessitates more labor for preparing and packaging parcels compared to simply delivering pallets to stores. Additionally, the industry grapples with a scarcity of candidates. Furthermore, warehouses are confronted with the colossal task of retaining trained resources, which entails making jobs more appealing. Financial compensation is no longer the sole criterion for attracting or retaining workers. Motivation and job satisfaction have emerged as stronger factors for drawing and keeping employees, as well as for improving their quality of work life. For employers, this entails taking tangible measures on two fronts. Firstly, they must provide a secure environment that prevents workplace accidents and musculoskeletal injuries. Secondly, they must ensure a certain degree of autonomy to foster job satisfaction among the workforce. To reinforce this aspect, employers are exploring additional initiatives, such as integrating challenges into business processes for younger employees from the “gaming” generation. For older employees, companies stand to gain by adapting their assigned tasks—by sparing them the most arduous jobs and heavier loads—and relying on their expertise to mentor younger staff. By addressing these issues, businesses can foster a sense of belonging for all employees.
Logistics professionals operate daily amid uncertainty due to fluctuating flows and absenteeism rates that can sometimes reach 50%. They must constantly maintain agility. It is their responsibility to organize on-site resources by prioritizing activities. This calculation of actual production capacity combined with optimizing the available workforce is a complex challenge. It can be alleviated through the implementation of an effective policy that promotes versatility, yielding benefits as detailed by Isabelle Badoc: “It guarantees increased flexibility for warehouses thanks to multi-skilled resources, which increases the ability to perform the most critical tasks on any given day.” Simultaneously, employees trained in multiple trades can switch jobs every two hours, mitigating the monotony associated with repetition. They can maintain their focus and performance throughout the workday, experiencing less fatigue or boredom, ultimately leading to increased motivation. As a consequence, the warehouse will rely less on temporary workers, reducing costs.
Until recently, many warehouse managers instinctively prioritized investments in mechanization and automation to enhance performance. Nevertheless, resource management based on improved planning while maintaining the same human-machine ratio can prove more effective. That is the objective of Generix’s Resource Management System (RMS) solution, Generix Resource Management. This solution analyzes performance, forecasts the time needed to complete each task, and subsequently aligns these two factors to plan and improve resource allocation. Additionally, the system is customizable, catering to the unique needs of each warehouse. Another important advantage is its ability to reduce work-related accidents and monotony. “RMS can achieve flexibility on logistics sites by supporting increased operator skills and versatility, helping them to perform new tasks efficiently,” explains Isabelle Badoc.
Integrating AI into an RMS solution provides robust resource planning capabilities, thanks to its predictive and optimization features. The synergy between humans and robots will undoubtedly continue to be the primary logistics model in the coming years. Perhaps experimenting with optimizing the use of existing resources is a simpler and less expensive performance lever before heavily investing in machinery. By considering such alternative solutions, warehouse managers can make informed decisions to enhance productivity, flexibility, and employee satisfaction in the ever-evolving logistics landscape.
France’s electronic invoicing reform relies on a Y-architecture, where Partner Dematerialization Providers (PDPs) play a central role in issuing and…
The B2B mandate in Germany, set to take effect on January 1, 2025, marks a crucial step in the European…
Following the October 15 announcement regarding the abandonment of the PPF development, the DGFIP and its partner AIFE are ramping…
Work with our team to build your ideal supply chain software stack and tailor it to your unique business needs.