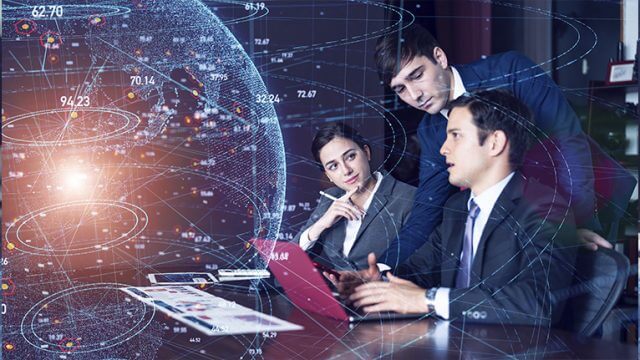
E-Invoicing and Its Geopolitical Stakes
France’s electronic invoicing reform relies on a Y-architecture, where Partner Dematerialization Providers (PDPs) play a central role in issuing and…
Generix Delivers Schematron for Electronic Invoicing to AFNOR to Ensure Interoperability Between PDPs Read the press release
As the Covid-19 crisis set, a crisis in the supply chain followed, triggered by people’s responses to the spread of the virus, such as panic buying, which submitted the supply chain to an unusual stress, and eventual disruption. As the situation evolved, it became clear that digital transformation and technology upgrades were actions that could not be delayed if you wanted to make decisions based on actual live data.
In preparing for the future, we shift from “responding to challenges” to proactive action. First and foremost, you need a selection of technology solutions that support scalable and transparent processes. There’s a lot of talk about predictive analytics and supply chain modeling solutions these days, but the first step in this process is always the implementation of operational management systems and data exchange systems.
By standardizing your processes and transforming your technology, you can create a system that lays the groundwork for staying ahead of the competition, improving efficiency and preparing for long-term growth. Here are a few ways to get started:
Food-related industries need to rely on a dynamic system that shows how your business is performing every day. It’s time to set goals for maintaining continuous quality control with your suppliers, within your own walls and in every part of the supply chain.
The first step is to look at all the software or technology you’re using now to see if you can consolidate or eliminate point solutions or irrelevant applications. Once you have a clear picture, you can ask if your systems can “talk” to each other and connect all decision data into a single source of truth. This helps eliminate siloed data and improves communication.
To give examples based on our company’s portfolio of solutions, the WMS system features automatic tracking of expiration dates, including residual expiration dates based on customer requirements. And personal customer accounts based on Generix Supply Chain Visibility provide data on availability products at various points in the supply chain, both in warehouses and in transit.
How many times has a document or other data been “lost” in email or file-sharing folders? How many times have you worked extra hours to put together a report manually from multiple spreadsheets?
It’s time to let technology take over most of your administrative and routine work. It’s time for the food industry to stop relying on paper, spreadsheets and other manual tools. Chapman’s Ice Cream was enabled to effectively track their ingredients throughout the supply chain thanks to automation, and thus had the data required to react quickly to changes in consumer preferences and protect food safety. During the early days of the pandemic, John Fleming reports in a recent webinar that Chapman’s used the real-time data provided by their WMS to anticipate the supply of their ingredients and manage their customers’ expectations accordingly.
It’s important to remember that modernization doesn’t exclude people from processes. It is the use of human-centered technology that reduces human error, reduces administrative work and improves results. Certainly, you will have to invest in innovation, but technology creates efficiency and transparency that will ultimately save you time and money. Chapman’s for example, were able to reduce losses by gaining real-time visibility over their inventory.
Generix offers its customers an end-to-end process implementation based on the Generix Supply Chain Hub solution. All modules of the solution are interconnected by an integration bus to which you can connect your accounting system (ERP) and other applications in use.
Integrating new suppliers and working with existing ones comes with many challenges. Emails go unanswered, contract renewal dates are often missed. Updating certificates, documents and audit results is a chore, to say the least. In addition, supply disruptions during the pandemic may have prompted you to diversify your supply chain. To summarize, working with suppliers is a lot of communication, paperwork and dates to keep track of. In addition, you are responsible for making sure your suppliers meet government and industry standards.
Using vendor relationship management software makes it easier for all parties, allowing everyone to work faster and more collaboratively. Supplier contacts, certification submittals and audit results are all centralized in one place, allowing you to work quickly and accurately to develop and renew contracts. Automated renewal reminders eliminate routine monitoring or worrying about updating a common Excel file on time.
Our company’s portfolio includes different level solutions to standardize work with suppliers: SCV based supplier accounts for goods and services, EDI based supplier portal solution, Generix Collaborative Replenishment for VMI based work. Our company methodology allows us to develop onboarding packages for fast integration of new vendors.
Modernization of systems makes sense both competitively and financially. However, in my opinion, the most compelling reason to upgrade is the well-being of your employees. In these volatile times, they are doing more with the same or even fewer resources, taking on more workload, which can lead to faster and harder burnout. If you can do more to support your employees and their effectiveness, you will achieve better results in the long run.
Generix Group North America provides a series of solutions within our Supply Chain Hub product suite to create efficiencies across an entire supply chain. From Warehouse Management Systems (WMS) and Transportation Management Systems (TMS) to Manufacturing Execution Systems (MES) and more, software platforms can deliver a wide range of benefits that ultimately flow to the warehouse operator’s bottom line. Our solutions are in use around the world and our experience is second-to-none. We invite you to contact us to learn more.
France’s electronic invoicing reform relies on a Y-architecture, where Partner Dematerialization Providers (PDPs) play a central role in issuing and…
The B2B mandate in Germany, set to take effect on January 1, 2025, marks a crucial step in the European…
Following the October 15 announcement regarding the abandonment of the PPF development, the DGFIP and its partner AIFE are ramping…
Work with our team to build your ideal supply chain software stack and tailor it to your unique business needs.