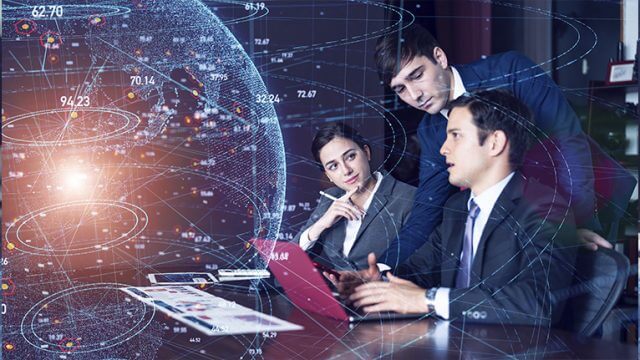
E-Invoicing and Its Geopolitical Stakes
France’s electronic invoicing reform relies on a Y-architecture, where Partner Dematerialization Providers (PDPs) play a central role in issuing and…
Generix Delivers Schematron for Electronic Invoicing to AFNOR to Ensure Interoperability Between PDPs Read the press release
The French Association for Logistics (ASLOG)1 estimates that the supply chain sector represents between 60 and 90% of the cost of products for companies. Unfortunately, a survey conducted at the end of 2020 by Longitude for Orange Business Services reveals that 40% of multinational supply chains were helpless in the face of the Covid-19 crisis.2 In response, 80% of them claim to have accelerated their digital transformation over the past several months. Automation, AI, the cloud and data analysis tools, of which Generix Group’s WMS and TMS solutions are a concentrate, are now seen as indispensable technological enablers to manage risks and develop greater responsiveness to fluctuating demands.
Transportation visibility is becoming a critical need for many organizations, regardless of size, geography or industry. Applications of real-time supply chain visibility technology are becoming increasingly valued by the consumer. With the advent of machine learning, visibility capabilities are now moving from “standard” to “predictive“, enabling greater process automation and more accurate and reliable ETA (Estimated time of arrival) forecasts.
Indeed, improving its logistic visibility allows :
● optimization of resources and transportation costs:
The visibility tool accurately tracks transportation operations, enabling better decisions based on reliable data. All delivery information is aggregated to measure delivery performance, analyze root causes of problems and determine areas for improvement. ● Generation of a higher NPS:
The Net Promoter Score is one of the most widely used indicators of customer satisfaction and loyalty. Platforms help improve customer satisfaction and optimize collaboration within an organization by informing internal teams and customers in advance of real-time status and predictive arrival of deliveries. ● Reduction of penalties due to delays or waiting times of carriers:
The algorithms use machine learning for increased accuracy. This allows to quickly anticipate problems on transport flows. The predictions help to effectively manage problematic situations and control their impacts. For example, if a factory is warned early enough that its supplier is facing a production problem or delivery delays, it will be able to find alternative sourcing, prioritize the launch of programs not dependent on the supply in question, etc.
As an example, Generix Group’s Supply Chain Visibility solution, designed for WMS and TMS users, is connected to tracking data from various carrier systems, such as Shippeo, whose algorithm includes 800 parameters, among which are listed all the hazards that impact the ETA: regulations, waiting time, dwell time, traffic, weather, trailer exchange, drivers’ break, etc. Thanks to these indicators, the visibility of the flows is considerably refined :
– up to 24 hours before delivery, the ETA is given with an accuracy of 85%;. – it reaches 90 % 12h before the delivery.
In this way, the product drop-off point (store, for example) is informed in real time of the arrival time, for optimized organization and pick-up.
As long as they themselves have a strong commitment to their customers, it is in the interest of all chain participants to give visibility to their partners: the unique approach of automated carrier onboarding, for example, is a proven method: the idea is to benefit from the carriers’ ecosystem. That’s why Shippeo remains 100% free and neutral for them and has a 98% satisfaction rate. This satisfaction emphasizes the speed, generated by the automation of administrative tasks, and the quality, especially of the services delivered by a dedicated support team.
Shippeo, a French company, has a strong international dimension. In total, the visibility platform supports deliveries in more than 75 countries, for a total of about 25 million deliveries per year.
Still with this idea of benefiting from the carriers’ ecosystem, Generix Group will release a smartphone application in summer 2022. This will enable the company to sharpen its tracking data and its drivers to update certain information, such as the delivery address if it is out of date, to optimize the next rounds.
1 francesupplychain.org 2 According to Real-time intelligence and the future of supply chains, orange-business.com
France’s electronic invoicing reform relies on a Y-architecture, where Partner Dematerialization Providers (PDPs) play a central role in issuing and…
The B2B mandate in Germany, set to take effect on January 1, 2025, marks a crucial step in the European…
Following the October 15 announcement regarding the abandonment of the PPF development, the DGFIP and its partner AIFE are ramping…
Work with our team to build your ideal supply chain software stack and tailor it to your unique business needs.