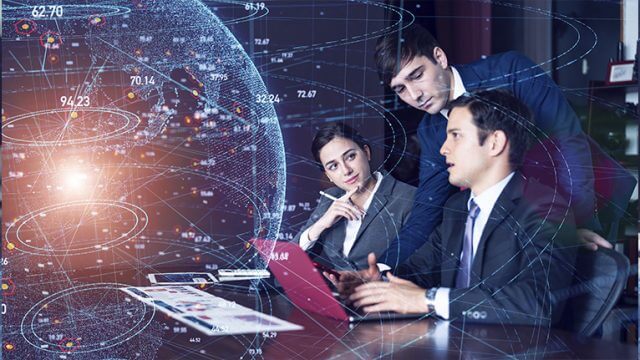
E-Invoicing and Its Geopolitical Stakes
France’s electronic invoicing reform relies on a Y-architecture, where Partner Dematerialization Providers (PDPs) play a central role in issuing and…
Generix Delivers Schematron for Electronic Invoicing to AFNOR to Ensure Interoperability Between PDPs Read the press release
Some credit the increase in recalls since 2013 to better inspections and testing.
Despite the recent decline in total U.S. food recalls, the Public Interest Research Group (PIRG) [pdf] notes that for meat and poultry, the most hazardous class of food recalls nearly doubled from 2013 to 2018.
These are Class 1 recalls, which involve foods for which “there is a reasonable probability that eating the food will cause health problems or death.” That definition comes from the US Department of Agriculture Food Safety and Inspection Service (USDA FSIS). The U.S. Food and Drug Administration (FDA) uses a similar standard.
The brands behind many of the big food recalls in 2017 and 2018 sustained real damage, even if their products weren’t at fault.
Good food traceability can’t guarantee your brand will never face a food recall. But it can help you reduce the risk of making things worse if one occurs.
Food brands with superior traceability systems are likely to fare better in recalls than brands without them.
You know the United States and Canada require a base level of food traceability. So does the European Union. But just meeting regulatory requirements doesn’t protect your brand from other risks related to food safety and product recalls.
What are the differences in food traceability systems that are just adequate and those that are superior?
Generix Group North America suggests 10 traits that distinguish one traceability system from another. The traits appear in the table that follows, along with a list of helpful questions about your current capabilities.
One of the more important traits of a good traceability system is its integration of your production-control and logistics systems.
Does your company need all these capabilities?
You’ll have a much clearer idea of what you have and what you need after you answer the questions in each category.
1. Compliance
Do your traceability capabilities comply with laws and regulations of all the countries, states, and provinces where your products are sold?
Do your current capabilities comply with the requirements of current and future customers? (Many big retailers require more traceability from suppliers, to limit their own liability in case of a recall.)
2. Speed & timeliness
If a food-safety emergency arises, how fast can you generate data to help determine whether your products are involved, and which ones?
If a regulator or a potential customer asks you to run a mock recall, how fast can you do it?
If an investigator asks how many customers have received shipments of a specific batch or lot, and where, how fast can you provide an accurate count?
Does your traceability reporting cover all your production for any period of time, including your current work-in-process production?
3. Accuracy, granularity & completeness
Would you bet your company on the accuracy of the data in your traceability system?
Do you use barcode scanning to ensure the accuracy of data and efficiency of operations at every touchpoint?
Can you accurately track all the ingredients, labels, and packaging materials that go into each batch or lot of shippable products?
Can you track which batches of ingredients, labels, or packaging materials are used in each lot of shippable products?
Can you track who in your operations touched a product or ingredient and the time at which each touchpoint occurred?
Can you accurately track and trace the expiration date of each batch of every product and all its ingredients?
Can you track how and where each product or ingredient was stored before and after manufacturing?
Can you accurately track and trace finished goods, ingredients, labels, and packaging materials through every step of receiving, warehousing, manufacturing, fulfillment, and shipping processes?
4. Efficiency
How much effort and disruption are involved in producing a full traceability report?
How many resources does the activity require?
How much does a mock recall disrupt your staff?
Does the difficulty or running mock recalls prevent you from running them at least once a quarter?
5. Control
Do your traceability processes enable you to prevent missteps that may compromise food safety? Is your traceability system linked to your execution systems?
Do your processes help ensure, for example, that your products are never cross-contaminated with undeclared food allergens?
Do your processes ensure that expired ingredients can’t be used in production processes?
Can they prevent your company from using compromised batches of ingredients in your production or shipping processes?
Do they prevent anyone from adding the wrong ingredients to a production batch?
Do your traceability processes prevent use of the wrong labels or packaging materials?
6. Direction & range
How far backward can you trace toward your sources of supply?
If you’re looking backward, can you go back to your suppliers’ suppliers?
Can you go back to the growers’ fields or the exact fishing boat that brought in the catch?
How far forward can you trace to the customer locations where you’ve shipped goods?
7. Reporting, analytics & alerts
How comprehensive are the reports and analytics? How easy are they to understand?
Does your reporting cover all of your production for any period of time, including today’s production?
8. Flexibility
Do your current solutions enable you to easily restructure or reconfigure your traceability capabilities when recipes, suppliers, or supply chains change?
How fast can you adapt your traceability systems when such changes occur?
How much effort does it take, and how much does it cost?
9. Integration
How well does the traceability system integrate with your current processes and information systems?
With your enterprise resource planning (ERP) system?
With your warehouse management system (WMS)?
With your manufacturing resource planning (MRP) system?
With your manufacturing execution system (MES)?
With your e-commerce systems?
How challenging and costly is it to maintain the integrations with all those other systems?
10. Technology
Does your current technology offer the flexibility and security you need to ensure operating efficiency, throughput, compliance, and risk reduction?
How much worse might a food recall be if you don’t have many of the capabilities listed in the table?
Would you like help to evaluate your food traceability needs? Or ideas to help you meet your needs?
If so, start a conversation with a food safety logistics consultant at Generix Group North America through conversations@generixgroup.com.
France’s electronic invoicing reform relies on a Y-architecture, where Partner Dematerialization Providers (PDPs) play a central role in issuing and…
The B2B mandate in Germany, set to take effect on January 1, 2025, marks a crucial step in the European…
Following the October 15 announcement regarding the abandonment of the PPF development, the DGFIP and its partner AIFE are ramping…
Work with our team to build your ideal supply chain software stack and tailor it to your unique business needs.