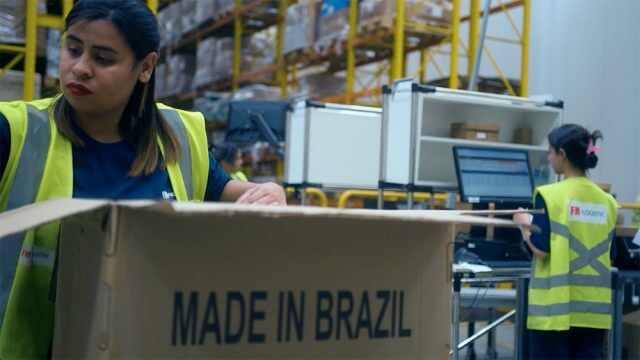
Generix WMS and FM Logistic Brazil simplify processes and increase efficiency in their 70,000 square meters of warehouses.
Transformation and Efficiency with Generix WMS Solution
Generix Delivers Schematron for Electronic Invoicing to AFNOR to Ensure Interoperability Between PDPs Read the press release
Analog Devices, Inc. defines innovation and excellence in signal processing. ADI’s analog, mixed-signal, and digital signal processing (DSP) integrated circuits (IC) play a fundamental role in converting, conditioning, and processing real-world phenomena such as light, sound, temperature, motion, and pressure into electrical signals to be used in a wide array of electronic equipment. ADI is synonymous with high performance among electronics manufacturers.
That means the clearest image, crispest sound, and optimum interface, size and performance in thousands of entertainments, medical, communications, industrial and other applications.
In today’s automobiles, digital still cameras, LCD and plasma televisions, cellular handsets, medical imaging devices, and factory automation equipment, ADI’s ICs enable continuous connections, more vibrant pictures, clearer sound, and increased portability. ADI’s core analog and DSP technology is quite literally everywhere.
Analog Devices became a Generix group client in 2012. The corporate headquarters and facilities are located in Norwood, MA and their regional headquarters are established in Germany, Ireland, Japan and China.
"The main benefit is that we have so many parts, and it told us where every piece and every item was. Before that, it was basically all memory and spreadsheets, and we had to keep track of everything manually. It was good because you didn’t need to keep track of anything manually and as soon as you would look something up it would pinpoint all the exact locations where the different pieces of a spare part were at – buildings, rooms and shelves. The support was good – they were right on it, they replied promptly. Didn’t take too long. They were very helpful too – any questions I had I could call or e-mail them at any time. They would always find the answer." Thomas Ryan Stockroom Group Lead
Find the full description of the solutions presented in this case study
"The main benefit is that we have so many parts, and it told us where every piece and every item was. Before that, it was basically all memory and spreadsheets, and we had to keep track of everything manually. It was good because you didn’t need to keep track of anything manually and as soon as you would look something up it would pinpoint all the exact locations where the different pieces of a spare part were at – buildings, rooms and shelves. The support was good – they were right on it, they replied promptly. Didn’t take too long. They were very helpful too – any questions I had I could call or e-mail them at any time. They would always find the answer."
Thomas Ryan
Stockroom Group Lead,
Transformation and Efficiency with Generix WMS Solution
Since 1922, Shorr Packaging Corp. has established itself as a major player in packaging in the United States. Faced with…
Emballages Carrousel, a leader in packaging solutions, embarked on an ambitious project to modernize its operations and meet the growing…
Work with our team to build your ideal supply chain software stack and tailor it to your unique business needs.