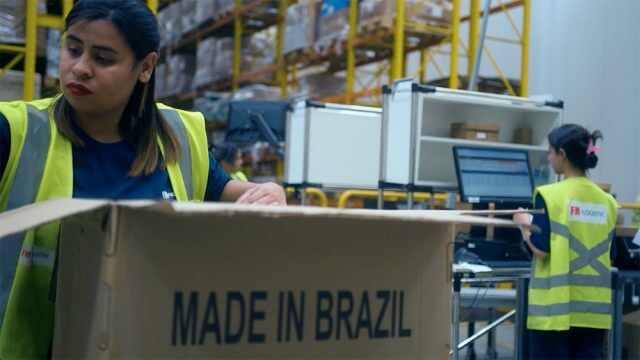
Generix WMS and FM Logistic Brazil simplify processes and increase efficiency in their 70,000 square meters of warehouses.
Transformation and Efficiency with Generix WMS Solution
Generix Delivers Schematron for Electronic Invoicing to AFNOR to Ensure Interoperability Between PDPs Read the press release
Hitachi Astemo Americas manufactures automotive materials, products, and systems for some of the most prestigious vehicule manufacturers in the world.
Hitachi’s Querétaro business unit, assembles critical parts for brake systems and car suspensions, including brake calipers, hoses, fittings, wiring harnesses, discs, and pads. The facility is approximately 1 million sq. ft., employs 200 to 1000 workers, and operates 24 hours a day, 7 days a week.
Hitachi Astemo acquired a new client: A global, best-in-class original equipment manufacturer (OEM) interested in the brake and suspension parts assembled in the Querétaro facility. After performing an audit of Hitachi’s facility, the client determined that systems presently in use would not be able to meet operational demands. The key challenges that Hitachi had to urgently address in the Querétaro facility were:
In addition to these issues, Hitachi had to contend with the same resource shortages that have been plaguing most manufacturers and distributors around the world. The manufacturer had to find solutions to avoid costly production delays caused by shortages and improve material requirements planning capabilities.
Hitachi Astemo launched a competitive RFP process to source a Warehouse Management System (WMS) that would help overcome current challenges. At the end of the RFP process, Hitachi identified the SOLOCHAIN WMS/MES as the solution of choice for the Querétaro facility.
Schedule Time is of the essence: Hitachi could not afford any delays and had to quickly implement solutions to meet the new client’s requirements. Leveraging SOLOCHAIN’s modular design, the Generix team divided the implementation into two phases to ensure that key capabilities were delivered on time.
Phase 1:
Implement SOLOCHAIN WMS/MES to support manufacturing processes in the brake department.
Phase 2:
Deploy SOLOCHAIN in the suspension department and complete the WMS/MES integration with Hitachi’s ERP system, client facing applications, and supplier systems.
Keys to Success
Thanks to Generix’s experience and expertise, the implementation team was able to develop creative solutions for problems that had never been encountered before, and to achieve a fully remote implementation during the first phase. That creativity, paired with a well-iterated and clearly defined deployment process, enabled the Generix Team to guide Hitachi’s engineers through the process and meet every deadline.
Hitachi’s management also contributed to the operation’s success by fully dedicating members of its technology team to the implementation. Hitachi’s technology experts collaborated with the Generix team and leveraged SOLOCHAIN’s easy-to-use implementation tools to navigate the implementation process with ease and agility.
Results
Meeting the Industry’s Most Stringent Standards and Opening Up New Channels SOLOCHAIN WMS/MES allowed Hitachi to implement warehouse management best practices in the Querétaro facility and to comply with client’s requirements as well as automotive OEM industry standards.
To meet the client’s quality assurance standards, Hitachi was required to enforce FIFO inventory management. With SOLOCHAIN WMS/MES, FIFO is now applied without fail at every step and for every item in stock: components, subassemblies, and finished goods.
Meanwhile, SOLOCHAIN’s powerful tracking capabilities have replaced error-prone spreadsheets. This ensures the manufacturer can perform efficient and targeted recalls the minute an item is identified as problematic.
Compliance with the industry’s strictest quality standards has opened up new possibilities for Hitachi. Thanks to SOLOCHAIN WMS/MES, the manufacturer can now explore new markets and extend the target audience in the high-end automotive OEM sector.
Accurate and Detailed Inventory Visibility – Improved Throughput: Significantly Faster Manufacturing Process Being able to rely on accurate inventory data enables Hitachi to stay ahead of demand and avoid frustrating shortages. SOLOCHAIN helps the manufacturer ensure sufficient quantities are always maintained as safety stock, for instance, which provides an additional a further guarantee to clients who might be concerned about product availability.
Optimized Item Locations and Accurate Picking Activities Made for a Better Work Environment Optimized item location and efficient task assignments mean that goods are being moved more efficiently across the facility. This, in turn, prevents frustrations on the floor and encourages employees to handle items with more care, which leads to a tidier warehouse and a better work environment.
A Better Customer Experience Shipping activities no longer rely on spreadsheets at the Querétaro facility. SOLOCHAIN WMS/MES now helps management plan and organize shipments to avoid bottlenecks at the dock and guarantee that every order is shipped on time.
Through integration with customer–facing applications, SOLOCHAIN provides information on the location and status of ordered items, helping clients track the progress of every order.
Transformation and Efficiency with Generix WMS Solution
Since 1922, Shorr Packaging Corp. has established itself as a major player in packaging in the United States. Faced with…
Emballages Carrousel, a leader in packaging solutions, embarked on an ambitious project to modernize its operations and meet the growing…
Work with our team to build your ideal supply chain software stack and tailor it to your unique business needs.