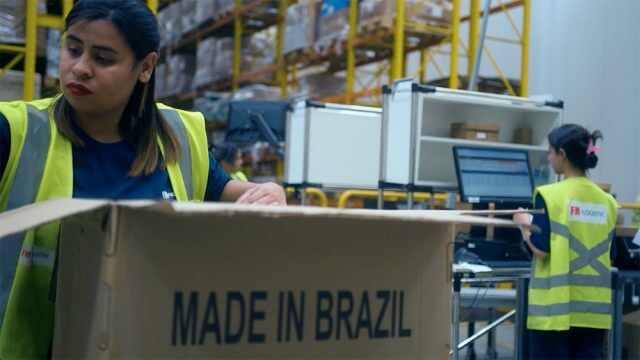
Generix WMS and FM Logistic Brazil simplify processes and increase efficiency in their 70,000 square meters of warehouses.
Transformation and Efficiency with Generix WMS Solution
Generix Delivers Schematron for Electronic Invoicing to AFNOR to Ensure Interoperability Between PDPs Read the press release
The Leroy Merlin branch of the ADEO Group is a major international player in the DIY retail market. The Leroy Merlin brand accompanies consumers all over the world to improve their lifestyle and quality of life. The 325 Leroy Merlin shops are located in 13 countries: Greece, Brazil, France, Italy, Poland, Portugal, Spain, Russia, China, Romania, Ukraine, Turkey and Cyprus. More than 50,000 employees worldwide work in Leroy Merlin shops.
Selecting a transport management solution
Having completed the Generix WMS, YMS and Supplier Portal implementation project, the Leroy Merlin Vostok team selected another module from Generix Supply Chain Hub’s SaaS platform as their transportation management system. Choosing Generix TMS module made the integration project possible in a shorter time and at a lower cost than implementing a third-party solution. It is also worth mentioning that maintenance of all implemented and new Generix systems was performed by the same team located in Moscow. This “one-stop-shop” format simplified and accelerated the interaction between key system users and the development team.
Along with other clear benefits, Generix TMS allows Leroy Merlin Vostok to improve billing management in automatic mode and simplify work with suppliers (punctuality, responsiveness, etc.). This includes significant benefits in terms of communication: it will be possible to accurately know the available stock on the road or on the ship, track items, balance activities at the point of sale and in the warehouse, and inform end customers.
Project objectives
The project involved commissioning Generix TMS at 6 Leroy Merlin Vostok sites with an existing Generix WMS.
The implemented system was to solve the following tasks:
How does a Saas-based TMS work?
“Choosing the SaaS model for supply chain management tools was key for us: it allowed us to gain time and flexibility in deploying the solution, launch operations in a very short time and gain economic visibility of our logistics information system,” said Bernard BARFETI, director of organization and information systems at Leroy Merlin Vostok.
It is a system which not only fully controls the transport operations in accordance with its algorithms (which can be modified as required), but also works in conjunction with a special web portal for carriers, to which all transport companies working with Leroy Merlin Vostok are connected.
The algorithms can be very diverse, the most common being “deliver in minimum time”, “deliver at minimum cost” or “deliver by specific mode of transport”. The system itself will select the carriers that meet this requirement.
All those who are closely associated with the delivery of goods often point out that finding a quality transport company is not easy. TMS helps here too: analyzing daily deliveries, quality, speed, cost, the system itself creates an internal rating and, if the algorithm is not entered into the other requirements, it chooses the most reliable contractors. In other words, the system becomes not just an “iron”, but a self-developing tool with elements of Artificial Intelligence.
Thus, it is a self-learning system which eliminates the human factor from the transport planning process and turns managers from “Excel and telephone” workers into true strategists who determine the optimal algorithm for a particular period of the year or for a particular logistics flow.
For example, in the period when numerous bulky deliveries have to be handled or a large volume of special vehicles has to be reserved – the manager puts all requirements into the automated system algorithm and realises all the company’s needs at any given time.
More details about the features of the web-portal integrated into TMS should be provided. This point is important, because in addition to simplicity, transparency and speed in matters of solving transportation tasks, here, on the portal, is formed and all documentation, which has always been a cause of headaches for managers. Transport bills of lading and other accompanying documents are also generated here on the portal. And while TMS is deployed in the cloud, the portal is essentially a website that can be used by any transport function provider.
Efficiency at the end of implementation
The customer noted the following changes in transport processes:
Optimisation of resources – at the push of a button, the system “schedules” jobs for transport companies.
Transparency in the process of selecting transport – due to a clear algorithm embedded in the program, it is always possible to explain why a particular carrier has been selected for a particular delivery.
Improved staff quality – the transport department doesn’t waste time on preparing and distributing tasks, but instead deals with exceptions, analyses results and coordinates with related departments and counterparties.
Find the full description of the solutions presented in this case study
Transformation and Efficiency with Generix WMS Solution
Since 1922, Shorr Packaging Corp. has established itself as a major player in packaging in the United States. Faced with…
Emballages Carrousel, a leader in packaging solutions, embarked on an ambitious project to modernize its operations and meet the growing…
Work with our team to build your ideal supply chain software stack and tailor it to your unique business needs.