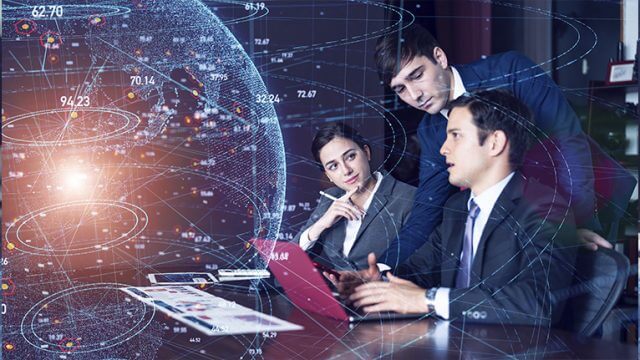
E-Invoicing and Its Geopolitical Stakes
France’s electronic invoicing reform relies on a Y-architecture, where Partner Dematerialization Providers (PDPs) play a central role in issuing and…
Generix Delivers Schematron for Electronic Invoicing to AFNOR to Ensure Interoperability Between PDPs Read the press release
Today, as highly efficient cloud-based technology solutions become more accessible, Food and Beverage companies of all sizes are discovering the means to digitize their operation. As a result, the technology landscape in the industry is changing at a dizzying pace. “Looking into the future, it’s about resiliency and an ability to adapt to changes in the marketplace and new business models,” IDC Manufacturing Insights’ Simon Ellis told MIT Sloan School. “If a competitor comes along with a next-generation, digitally fueled capability, [companies] need to find a way to avoid being disrupted.”
A recent report by Gartner, Inc. confirmed the trend, revealing that more than half of the operators they had surveyed now believe technology solutions essential to their capacity to compete. In the same report, Gartner’s analysts indicated that at least half of global product-centric companies were likely to invest in real-time transportation visibility platforms by 2023.
To stakeholders in the Food and Beverage industry, that last bit of information may seem like a conservative prediction. Supply chain operators who deal every day with expiration dates and customer specific requirements know all too well how a company’s success hinges on its capacity to maintain accurate and real time visibility over inventory and products.
Not a surprise, then, that more and more Food & Beverage companies are turning to technology solutions like the SOLOCHAIN WMS/MES to obtain the kind of inventory visibility that enables the operational agility needed to meet their productivity targets.
Quickly evolving demand patterns and the emergence of new purchasing habits have made things much more complicated for Food & Beverage companies. Supply chain operators can no longer ignore the pressure to open new channels if they intend to satisfy the needs of their wholesale clients as they strive to meet the complex demands of individual customers: same day delivery, BOPIS, BORIS, etc.
The first thing Food & Beverage companies must do to achieve the kind of omnichannel efficacy that enables competitivity and growth is to implement solutions that gives them the flexibility to quickly adjust and adapt their order fulfillment workflows. A powerful solution like SOLOCHAIN, the only WMS in Gartner’s Magic Quadrant to boast native MES capabilities, goes a long way to provide the supply chain visibility and flexibility operators need.
Thanks to its powerful inventory management capabilities, the SOLOCHAIN WMS provides Food & Beverage companies real time information on all item’s location across their entire supply chain, both within and beyond the walls of their facilities. With inventory accuracy rates above 99%, SOLOCHAIN ensures that all items are easily located and better managed.
Meanwhile, the SOLOCHAIN WMS enables companies to break down the communication silos of legacy supply chain systems. The dynamically updated data is presented on intuitive interfaces that are available to all employees across the company’s operation, from the back office to the warehouse floor – through mobile devices, for instance. Any and all inventory modifications are therefore immediately communicated to all interested parties.
However, when it comes to operational agility and end-to-end supply chain collaboration, SOLOCHAIN truly sets itself apart from other WMS solutions thanks to its fully integrated MES capabilities.
SOLOCHAIN’s native MES functionalities are a boon to all Food & Beverage companies that manage any type of Work Order related activities – kitting, assembling, manufacturing, production, repacking, etc. By seamlessly integrating WMS & MES capabilities, SOLOCHAIN makes it easy for operators to track raw materials, components, packaging materials, and finished goods. That, in turn, enables them to efficiently adapt all processes and workflows when disruptions or changes in the demand signal demand it. Needless to say, this turns out to be a huge advantage in an industry so sensitive to expiration dates and customer specific requirements.
A soup making company, for example, can use SOLOCHAIN to manage inventory allocations and ingredient picking jobs at the same time as it leverages the system’s MES capabilities to ensure that the best inventory (FIFO, FEFO, or UOI) is being consumed throughout the production process. Meanwhile, the integrated WMS/MES hub also facilitates the management of scraps and waste. Should an employee mishandle a case of tomatoes during the production process, making the fruit unusable, they can report the loss on their mobile devices. The system’s Scrap/Waste process then immediately generates priority replenishments, to ensure that the soup production process continues uninterrupted.
The seamless integration of SOLOCHAIN’s WMS/MES capabilities also dramatically improves the company’s capacity to trace every item and ingredient consumed in the soup making process. Item traceability reports allow the company to track ingredients and finished goods, forwards and backwards, from suppliers to customers. Should a specific lot of carrots eventually be identified as problematic, the company can quickly put all the problematic ingredients and produced soup lots “On Hold”. Meanwhile, thanks to detailed and accurate Item/Lot Number data, SOLOCHAIN immediately identifies the affected suppliers and customers, making it quick and easy for the company to issue the appropriate recalls.
These are just some of the ways in which the SOLOCHAIN WMS/MES affords the soup making company the visibility and agility to anticipate on problems, rapidly adapt its workflows and processes, and improve throughput. Generix Group North America provides a series of solutions within its Supply Chain Hub product suite to create efficiencies across a company’s entire supply chain. Our solutions are in use around the world and our experience is second-to-none. We invite you to contact us to learn more.
To learn more download the WMS Solochain Product Sheet Here.
France’s electronic invoicing reform relies on a Y-architecture, where Partner Dematerialization Providers (PDPs) play a central role in issuing and…
The B2B mandate in Germany, set to take effect on January 1, 2025, marks a crucial step in the European…
Following the October 15 announcement regarding the abandonment of the PPF development, the DGFIP and its partner AIFE are ramping…
Work with our team to build your ideal supply chain software stack and tailor it to your unique business needs.