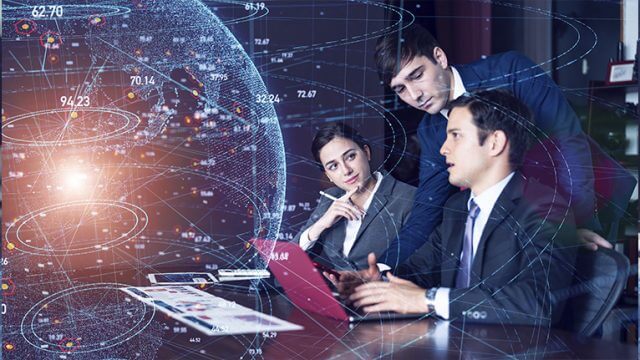
E-Invoicing and Its Geopolitical Stakes
France’s electronic invoicing reform relies on a Y-architecture, where Partner Dematerialization Providers (PDPs) play a central role in issuing and…
Generix Delivers Schematron for Electronic Invoicing to AFNOR to Ensure Interoperability Between PDPs Read the press release
How do companies manage hazards in logistics? What level of visibility do they have over operational risks? What are the consequences of poor risk management? A study conducted by Generix Group on 145 companies working in the supply chain brings to light several points. Speaking strictly in terms of risk management, 64.6% of companies receive alerts when internal events occur and 39.4% of these companies regularly analyze operational risks by using different protocols. These figures show that decision-makers are well aware of the importance of having information on the problems they encounter in their logistics services. By analysing operational risks, you can implement effective processes for hazard anticipation and risk crisis management. Data collection can also be extended to include all supply chain operations. When information sharing is facilitated among all network partners, alerts from external players can also be brought to the company’s attention. With regards to the visibility companies have on hazards, the study reveals that companies maintain real-time relationships most notably with their customers. However, these types of relationships are less developed with carriers, freight forwarders and suppliers. Even though companies most often rely on Electronic data interchange (EDI), we can see that the market is far from being saturated: it still hasn’t been implemented by everyone.
Lastly, according to a large majority of respondents, the consequences of poor operational risks management are mainly of a financial nature. They generate:
● direct costs as a result of reimbursements and fees (for 58% of respondents); ● indirect costs as a result of legal disputes (for 61% of respondents).
According to 45% of companies, poor crisis management can damage a company’s e-reputation and image, a situation which is particularly detrimental to companies that sell their products online.
With the IoT (Internet of Things) and Big Data, information has never been as rich and accessible as it is today. RFID sensors and other connected objects can record a wide range of information such as the temperature or the geolocalization of trucks via GPS. The data collected by operators can be stored in a cloud and used by different players in the logistics chain. Thanks to platforms of interconnected data, we can have visibility over the entire ecosystem.
On the same topic: What if the future of the Supply Chain lied in a platform-enabled ecosystem?
By using artificial intelligence (AI) to analyze this information and building databases, companies can feed information to predictive systems used in logistics and transports to anticipate operational risks and thus make the right decision when faced with hazards. By processing this data, we can do the following:
● easily predict storage capacity and optimally find or build inventory; ● perfect the management of logistics resources; ● steer operations in real time.
With these predictive features, companies can process last-minute orders based on priority, an option that gives them a huge advantage. Information on the delivery of goods will be used to optimize ongoing operations (sharing transport means, optimizing delivery routes, etc.). In addition, having better information on road traffic allows you to calculate the arrival time of goods and transmit this information to customers so they will know precisely when their shipment is expected to arrive. Some companies also plan on using geolocalization to anticipate loading operations before trucks arrive on site.
Read also: Optimization of transport costs: the TMS in the front line
Even more so than internal data, external information has become for companies a strategic element in their search for enhanced performance. The goal is to collect as much information as possible about the external events that can disrupt company operations. This information is analyzed and then used for predictive analytics.
In terms of customer satisfaction, the challenge lies in collecting data from partners in order to analyze it in real time. The entire logistics chain must engage in information sharing if the benefits are to reach all levels. Let’s not overlook the reason why we analyze data collected from the ecosystem is so we can use it to identify operational risks that may have a negative impact on customer experience. Therefore, collaborating with the customer and the carrier on the same platform is essential if we want to be able to make the right decision and limit customer dissatisfaction in the event of disruptions.
France’s electronic invoicing reform relies on a Y-architecture, where Partner Dematerialization Providers (PDPs) play a central role in issuing and…
The B2B mandate in Germany, set to take effect on January 1, 2025, marks a crucial step in the European…
Following the October 15 announcement regarding the abandonment of the PPF development, the DGFIP and its partner AIFE are ramping…
Work with our team to build your ideal supply chain software stack and tailor it to your unique business needs.