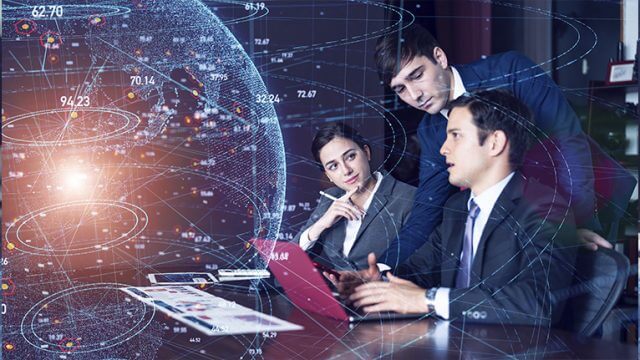
E-Invoicing and Its Geopolitical Stakes
France’s electronic invoicing reform relies on a Y-architecture, where Partner Dematerialization Providers (PDPs) play a central role in issuing and…
Generix Delivers Schematron for Electronic Invoicing to AFNOR to Ensure Interoperability Between PDPs Read the press release
As a result, food and beverage companies are struggling to maintain cost structures. These supply chain organizations are seeking to make smarter use of their distribution, fulfillment and shipping strategies to stay efficient and competitive—often in the face of adding new distribution channels in the fast-growing direct-to-consumer (DTC) e-commerce sector.
The lessons learned from the pandemic has sent food & beverage brands out to reduce risk by increasing manufacturing capacity to avoid stock-outs while increasing the speed of their supply chains.
Brands of all stripes are also adopting multi-warehouse strategies by positioning stock at distribution points closer to end customers across multiple DCs. By placing stock across multiple facilities, whether warehouses, DCs, or even microfulfillment centers and stores, shippers and their 3PL partners can still have a single repository of information with insights into real-time data and the ability to easily locate and track inventory and transfer stock across locations.
To accomplish this—against the backdrop of today’s accelerated pace to digitize supply chains—many companies are greatly reducing or eliminating manual or paper-based processes by turning to more advanced inventory management and warehouse management systems which connect to MES, ERP and other enterprise systems to bring a big-picture view into the supply chain.
With digitized information flows across facilities, solutions such as SOLOCHAIN WMS, an advanced SaaS warehouse management system, means supply chain organizations can achieve high levels of inventory accuracy and optimize stock across locations to better position against dynamic demand and supply patterns.
Likewise, pooled warehousing is another strategy that supply chain organizations are considering which helps companies reduce product storage costs by sharing resources. One benefit can be high service quality especially when like products with similar storage requirements are managed under one roof or across a set of facilities. A pooled warehouse is one that is shared among several parties, such as manufacturers, logistics providers or distributors in order to share space, resources and logistics information to improve the performance of the overall distribution process, as defined in a 2017 study published in Computers & Industrial Engineering.
The agricultural processing business is closely tied to the food & beverage industry, given the level of compliance to food safety requirements. Yakima Chief Hops (YCH), an all grower-owned network of family-owned hop farms headquartered in Yakima, Wash., is no exception. The largest hop company in North America, it distributes product from facilities in Yakima, Sunnyside, Calif., and Belgium.
YCH needed complete traceability, control and visibility into its products from “farm to kettle,” given its beer industry niche in serving many of the world’s finest brewers. In addition to commercial brewers and distributors, the company has a growing DTC e-commerce business serving home brewers.
In turn, its commercial brewer customers have their own requirements involving contracting, inventory accuracy, and packaging. By implementing SOLOCHAIN WMS, with integration into Sage X3 ERP as well as Magento e-commerce, overnight YCH drastically reduced its paper processes. Instead, warehouse staff use scanning guns and a QR code system, rendering the ability to store great amounts of data within the same barcode.
The net result? That automation alone reduced costs at YCH by about 35% from the prior manual system, along with the added efficiencies of eliminating thousands of carton transfers that it used to do under the old system before shipping out to customers. Further, order turnaround times for ecommerce orders went from days to 24 hours or less. YCH is also able to stay ahead of the changing food & beverage supply chain since the pandemic.
Learn more by downloading our eBook Post-Pandemic Impacts on Food & Beverage Companies.
To be sure, digitization of the supply chain and the painful lessons learned from the COVID-19 pandemic are bringing supply chain management into a new stage to reduce risk and gain efficiencies. Combined with digital inventory and warehouse management systems, multi-warehouse strategies and pooled warehousing are proven methods to improve supply chain performance while gaining efficiencies.
To learn more about SOLOCHAIN WMS, visit the video page.
Generix Group North America provides a series of solutions within our Supply Chain Hub product suite to create efficiencies across an entire supply chain. Our solutions are in use around the world and our experience is second-to-none. We invite you to contact us to learn more.
France’s electronic invoicing reform relies on a Y-architecture, where Partner Dematerialization Providers (PDPs) play a central role in issuing and…
The B2B mandate in Germany, set to take effect on January 1, 2025, marks a crucial step in the European…
Following the October 15 announcement regarding the abandonment of the PPF development, the DGFIP and its partner AIFE are ramping…
Work with our team to build your ideal supply chain software stack and tailor it to your unique business needs.