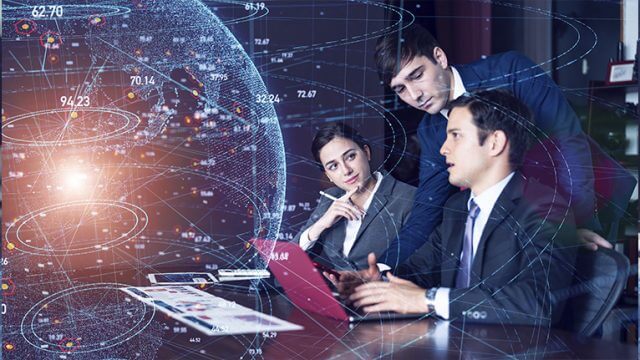
E-Invoicing and Its Geopolitical Stakes
France’s electronic invoicing reform relies on a Y-architecture, where Partner Dematerialization Providers (PDPs) play a central role in issuing and…
Generix Delivers Schematron for Electronic Invoicing to AFNOR to Ensure Interoperability Between PDPs Read the press release
Real-time inventory tracking is essential for maintaining accurate and up-to-date records of stock levels, locations, and movements within the warehouse. This feature ensures that businesses can:
Real-time inventory tracking allows businesses to continuously monitor stock levels to avoid stockouts and overstock situations. This ensures that inventory levels are always optimal, preventing lost sales due to stockouts and reducing the costs associated with excess inventory. With accurate stock level data, businesses can plan better for demand fluctuations and ensure that they have the right amount of stock at all times.
Accurate inventory data is crucial for fulfilling orders correctly. Real-time tracking ensures that the information used for order picking, packing, and shipping is up-to-date. This minimizes the risk of errors, such as picking the wrong items or quantities, leading to higher order accuracy and customer satisfaction. The accuracy provided by real-time tracking also helps in managing returns and exchanges more efficiently.
Access to current inventory data allows managers to make informed decisions regarding restocking and inventory management. Real-time visibility into stock levels and movements helps in identifying trends and patterns, enabling proactive management of inventory. This capability supports better planning and forecasting, ensuring that businesses can meet customer demand effectively without overcommitting resources.
Automated order management streamlines the processes of order picking, packing, and shipping, which minimizes errors and increases efficiency. Key aspects include:
Automated systems guide warehouse staff to the correct locations for picking items, reducing errors and speeding up the process. By using technologies such as barcode scanning, RFID, and voice picking, WMS software ensures that the right items are picked in the correct quantities. This reduces the time taken for picking and improves overall efficiency.
Automation in packing and shipping ensures that orders are packed correctly and shipping labels are generated automatically. This reduces the chance of mistakes, such as incorrect packaging or labeling errors, which can lead to shipping delays and customer dissatisfaction. Automated systems also help in optimizing packaging materials and processes, reducing costs and improving sustainability.
The ability to tailor workflows to match the specific needs of different clients or products enhances flexibility and efficiency. Customizable workflows allow businesses to implement best practices and standardize processes across different warehouse operations. This customization ensures that the WMS can adapt to unique business requirements and operational changes without significant disruptions.
Advanced reporting and analytics provide real-time data access and performance metrics crucial for informed decision-making. Features include:
Tracking key performance indicators (KPIs) such as order accuracy, on-time delivery, and inventory turnover is essential for evaluating warehouse performance. Advanced reporting tools in WMS software provide detailed insights into these metrics, helping businesses identify areas for improvement and optimize operations.
Generating reports tailored to specific business needs provides insights into various aspects of operations. Customizable reports allow managers to focus on the most relevant data, enabling more targeted analysis and decision-making. This capability supports continuous improvement initiatives and strategic planning.
Using analytics to identify trends, forecast demand, and optimize workflows improves overall efficiency and strategic planning. Data-driven decisions help businesses respond more effectively to market changes, customer preferences, and operational challenges. Advanced analytics also support predictive maintenance and other proactive measures, reducing downtime and improving reliability.
Seamless integration with other business systems, such as ERP (Enterprise Resource Planning) and TMS (Transportation Management Systems), is vital for unified operations. Important integrations include:
Synchronizing financial and inventory data with ERP systems reduces manual data entry and minimizes errors. Integration with ERP systems ensures that all business functions are aligned and operating from a single source of truth. This improves overall efficiency and accuracy in financial reporting, inventory management, and other critical operations.
Optimizing shipping and logistics operations by providing a unified view of the entire supply chain is essential for modern warehouse management. Integration with TMS systems allows for better coordination between warehousing and transportation functions, improving delivery times and reducing shipping costs. This integration also supports real-time tracking and visibility of shipments, enhancing customer service.
Real-time updates on order statuses and inventory levels enhance customer experience and operational efficiency. Integration with e-commerce platforms ensures that online orders are processed quickly and accurately, reducing the likelihood of errors and delays. This integration also supports seamless returns processing and inventory updates, improving overall customer satisfaction.
A WMS must be scalable and customizable to grow with the business and adapt to changing needs. Features supporting scalability and customizability include:
The ability to scale up or down based on transaction volumes and user numbers without significant performance degradation is crucial for a WMS. A flexible architecture ensures that the system can handle varying levels of demand and operational complexity, supporting business growth and adaptation to market changes.
Tailoring workflows, reporting tools, and user interfaces to meet specific business needs ensures that the WMS can adapt to unique operational requirements. Customizable workflows support process standardization and continuous improvement, allowing businesses to implement best practices and respond to changing conditions effectively.
Support for centralized management of multiple warehouses ensures seamless coordination and optimization across all locations. Multi-warehouse management capabilities allow businesses to distribute inventory efficiently, reduce transportation costs, and improve delivery times. This feature also supports centralized reporting and analytics, providing a comprehensive view of warehouse operations.
Effective labor management capabilities are essential for optimizing workforce productivity. Key features include:
Ensuring tasks are evenly distributed among workers helps avoid bottlenecks and improve efficiency. Workload balancing tools in WMS software help managers allocate tasks based on worker availability, skills, and current workload, ensuring that resources are used effectively.
Monitoring and analyzing employee performance helps identify areas for improvement and reward high performers. Performance tracking tools provide insights into individual and team productivity, supporting performance management and development initiatives.
Prioritizing tasks based on urgency and importance ensures that critical operations are completed first. Task prioritization tools help managers allocate resources to the most important tasks, improving overall efficiency and meeting customer expectations.
Cloud-based WMS solutions offer flexibility, scalability, and cost-effectiveness. Benefits include:
Accessing the WMS from anywhere with an internet connection enables remote management of warehouse operations. Cloud-based solutions support real-time visibility and collaboration, allowing managers and staff to work from different locations seamlessly.
Easily scaling the system to meet increased demand without significant capital investment in hardware is a major advantage of cloud-based WMS solutions. This scalability supports business growth and adaptation to market changes without the need for costly infrastructure upgrades.
Benefit from automatic updates and improvements, ensuring the system is always running the latest software version. Regular updates provide access to new features, security enhancements, and performance improvements, ensuring that the WMS remains effective and secure.
Integrating IoT devices into the WMS enhances visibility and control over warehouse operations. Benefits include:
Tracking the condition of goods, equipment efficiency, and other critical factors in real time improves operational visibility. IoT devices provide data on temperature, humidity, and other environmental conditions, helping businesses ensure the quality and safety of their products.
Using IoT data to predict and prevent equipment failures reduces downtime and maintenance costs. Predictive maintenance tools analyze data from IoT devices to identify potential issues before they become critical, supporting proactive maintenance and reducing unplanned downtime.
Dynamically adjusting storage locations and automating inventory replenishment based on IoT data optimizes warehouse operations. IoT connectivity supports real-time decision-making and automation, improving efficiency and reducing operational costs.
To successfully implement WMS software, follow these steps:
France’s electronic invoicing reform relies on a Y-architecture, where Partner Dematerialization Providers (PDPs) play a central role in issuing and…
The B2B mandate in Germany, set to take effect on January 1, 2025, marks a crucial step in the European…
Following the October 15 announcement regarding the abandonment of the PPF development, the DGFIP and its partner AIFE are ramping…
Work with our team to build your ideal supply chain software stack and tailor it to your unique business needs.