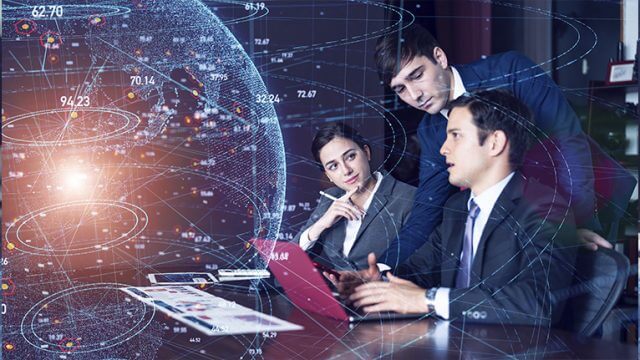
E-Invoicing and Its Geopolitical Stakes
France’s electronic invoicing reform relies on a Y-architecture, where Partner Dematerialization Providers (PDPs) play a central role in issuing and…
Generix Delivers Schematron for Electronic Invoicing to AFNOR to Ensure Interoperability Between PDPs Read the press release
How would you define warehousing resiliency? How can companies achieve it?
Resiliency in a warehouse is multifaceted. Labor, inventory, physical equipment, and warehouse management systems all play a part in the resiliency of a warehouse. How to achieve resilience is dependent upon the level of agility and flexibility a warehouse currently has. Achieving resilience requires an evaluation of all facets listed above to assess their flexibility and determine weaker areas to be addressed. Often there are process gaps which are closed via tribal knowledge and manual workarounds. The evaluation and documentation of the processes and the system will identify these gaps which can then be addressed to achieve resilience. Embracing and accelerating digital transformation initiatives is a great starting point. This could include:
The key to resilience is proactively planning and enabling agility to minimize the impact of a disruption while addressing changing conditions for future performance.
What are the major challenges of inventory management in 2021? How can companies overcome them?
The COVID-19 pandemic has shone a light on supply chains and on some of the fragility manufacturers and retailers face in fulfilling consumer demand. Changes in demand patterns have been pervasive, from panic buying of essential goods to reduced demand for luxury goods. These shifts caused shortages in some areas and excesses in others. To overcome the inventory management challenges companies have diversified their supplier networks removing single points of failure.
In addition, the just-in-time approach is to be reassessed. Disruptions in the timeliness of delivery impact production capabilities needed to meet the changing demands. Addressing such challenges requires greater transparency, visibility, and cooperation throughout the supply chain.
How can a WMS help fulfill ecommerce orders/address growing omnichannel challenges?
Omnichannel commerce unifies any/all customer contact points to construct a seamless and consistent customer journey. Whether conducted from a PC, a mobile device or in store, the customer experience is to be personalized and stay consistent. In turn, the omnichannel commerce impacts the distribution center as inventory is no longer segmented or reserved for a given channel. The WMS plays a key role in omnichannel fulfillment with inventory availability, control and flexible execution processes in place to satisfy the variable channel demands. Manufacturers, retailers and wholesalers enjoy direct-to-consumer shipment, wholesale flows, and retail replenishment consolidated with BOPIS (buy online pick-up in the store) delivering to a single destination. Flexible and configurable WMS solutions enable these variable flows to be executed within a single facility and maximize the utilization of inventory within the distribution facility or network.
How can the manufacturers enable a touch-free fulfillment environment?
Touch-free or touchless environment often referred to as Dark Warehousing is a concept that has been around only for a few years. Technology advancements around artificial intelligence and robotics can turn dark warehousing into reality, however for most operators this will not be a viable option for at least another decade. The focus of many operators is to maximize automation to reduce human dependencies, and therefore, gain efficiency. However, achieving total automation has proven to be elusive. The path to automation is built upon integration of automation equipment such as AS/RS, conveyors, sorters and robotics along with the Warehouse Management Systems and other supply chain solutions. The WMS has the complete picture of supply and demand with inventory and orders tracked perfectly. The system generates the tasks needed to be completed to fulfill the orders with the inventory on hand. Integrating the automation subsystems will reduce the number of touches and increase the level of throughput and predictability, thus allowing operators to meet customer expectations while reducing the costs of fulfillment of individual orders.
What drives organizations to turn to WMS this year?
Organizations that have not previously deployed a robust WMS with extended functionalities are now considering the advantages of doing so in response to the changes brought about the pandemic. Advanced WMS systems, like Generix Group’s Solochain WMS, enable warehouse operators and distributors to address head-on the changing nature of digital commerce post-Covid-19, which has collapsed the time and distance between customers and the rest of the supply chain.
Generix Group North America provides a series of solutions within our Supply Chain Hub product suite to create efficiencies across an entire supply chain. Our solutions are in use around the world and our experience is second-to-none. We invite you to contact us to learn more.
France’s electronic invoicing reform relies on a Y-architecture, where Partner Dematerialization Providers (PDPs) play a central role in issuing and…
The B2B mandate in Germany, set to take effect on January 1, 2025, marks a crucial step in the European…
Following the October 15 announcement regarding the abandonment of the PPF development, the DGFIP and its partner AIFE are ramping…
Work with our team to build your ideal supply chain software stack and tailor it to your unique business needs.