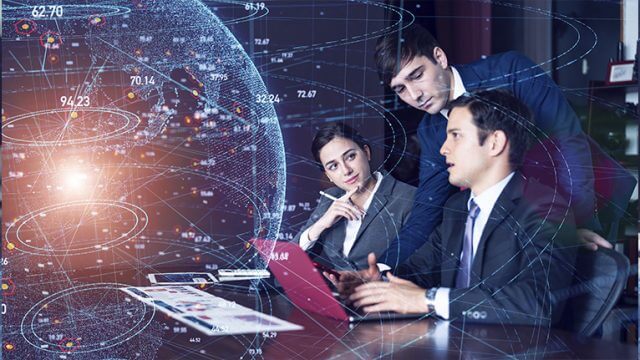
E-Invoicing and Its Geopolitical Stakes
France’s electronic invoicing reform relies on a Y-architecture, where Partner Dematerialization Providers (PDPs) play a central role in issuing and…
Generix Announces New AI-Powered Resource Management System (RMS) to Intelligently Optimize All Warehouse Resources Read the press release
The logic of the storage phase also applies to the preparation phase. In traditional warehouses or warehouse areas, preparation is practiced at the bottom of the rack: the reserved slots are located high up with full pallets, while the lower slots are occupied by pallets to be withdrawn individually or on a package-by-package basis. To maximize the performance of the preparation, the correlation between demand and organization is fundamental in the Warehouse Management System (WMS). And the picking management system must be fully adapted to the type of sales. For this, the WMS will therefore propose to manage prepared picking slots in a “fixed” or “temporary” way. In all cases, these management methods remain complementary in order to adapt operations to market needs. This is why “temporary” picking can become “fixed”, for example when the demand associated with the product decreases over the days or seasons.
Fixed picking, which is particularly appropriate in a linear type of organization, is associated with a preparation path corresponding to the logical requirements of traffic in the aisles. Its objective is to optimize the movements or the constitution of the preparation support, or the layout in the tray or the package. This allows, ultimately, to avoid a break in the loading rhythm at the end of the preparation process or upon arrival at the customer’s premises. In other words, from the outset, we prioritize the preparation of an order in a single package to the extent that this is possible. This avoids having to pack orders again at the end of the preparation process or sending them in two packages when one would have been sufficient. The creation of circuits is defined by the inventory manager according to customer needs. It respects rules related to products: category, family, weight/volume, rotation, etc. However, a multitude of possible combinations can be used to optimize their constitution and promote their complementarity. It is then that algorithms take on their importance in the WMS, so as to give the manager visibility on the strategic load/capacity tandem. The final step: a path is established on the basis of the analysis of data relating to the warehouse’s life cycle by combining available space and product type, depending on demand. When the products are stored in reception, we will use other calculations to propose reserve slots as close as possible to the picking slot corresponding to each reference.
With temporary picking or picking “under duress”, we recalculate the implementation of picking processes dynamically during the processing of a preparation cycle bearing in mind the following constraints:
Algorithms will then be put in place to implement picking processes matching each reference in the most appropriate way. This approach is very effective for managing relatively small product reference groups, which are in very high demand for a limited period. This is the case, for example, when launching a new collection or a special offer. Massification or “batch picking”
“Batch picking” or massification is a method of preparing orders which is characterized by the simultaneous withdrawal of several units with the same SKU code for different orders. Specifically, the preparer uses a preparation trolley on which will be placed “n” recipients corresponding to “n” different orders. He will then be able to distribute the same reference on several orders at the same withdrawal point, thus minimizing his movements. To help the preparer, an algorithm will calculate the breakdown of missions so as to find the optimal method of grouping them together. This principle is particularly used in e-commerce and textile sectors which handle a lot of small orders (between 1 and 3 pieces in general).
We can distinguish four main types of missions for a forklift operator:
These missions can be combined or crossed. When this is the case we use the term interleaving. A great source of productivity lies in the combination of storage missions with pallet removal missions. Most frequently, we will combine two missions with drop-off and pick-up points in the same aisle. These strategies are particularly effective in so-called very narrow aisle (VNA) storage areas because the turret truck vehicles used in them are slower. They are also absolutely crucial when using Automated Guided Vehicles (AGVs) whose traveling speeds are particularly slow. It is also possible to calculate the establishment of the missions according to a distance calculation algorithm. This functionality is implemented by configuring a distance calculator. This consists of setting up benchmarks and links between storage aisles in order to calculate the length of the journey between two storage points, which may be located in different aisles.
Triangulation is a method used for measuring distances on a human scale. This is a process of determining a distance by calculating the length of one side of a triangle, and measuring two angles of that triangle using trigonometric entities. The WMS is inspired by it to apply it to warehouse management and thus optimize the trips by applying the most direct paths possible. Triangulation is optimal in a radio frequency context. Indeed, scenarios ensure the automatic generation of missions by triangulation for forklift operators or dispatchers. In this case, the WMS algorithms will operate on the basis of several elements:
The WMS also knows how to calculate an intelligent allocation of docks at two key moments.
With this operating mode, the WMS will be able to synchronize flows of different kinds (single or multi-order, etc.). This will allow it to dynamically assign a final loading dock when validating the supports at the end of the preparation process. The algorithm will then take into account the state of congestion of the docks while checking the consistency criteria (customers, delivery dates, orders). We also use methods based on algorithms to fill the trucks as fully as possible. This work is done most of the time in collaboration with the TMS.
The concept of cross-docking consists of redistributing products in reception directly to a shipping dock without going through a storage phase. The algorithms of the WMS can operate using two tables. In the case of very long warehouses which are not designed as platforms for cross-docking, we will favor the intelligent allocation of receiving and/or dispatching docks, so as to bring them closer together and thus minimize travel distances. In the case of product references in reception which are also in stock, the WMS can implement more sophisticated algorithms which will take into account several parameters.
Note: we can serve a “spontaneous” need using a pallet received at the dock. The system is also authorized to be used at the dock in order to avoid a succession of different transfers (the aim is to minimize “load breaks”). In this case, we can decide not to respect the FIFO (First In First Out) order. The system checks compliance with expiration dates and “date contracts”.
France’s electronic invoicing reform relies on a Y-architecture, where Partner Dematerialization Providers (PDPs) play a central role in issuing and…
The B2B mandate in Germany, set to take effect on January 1, 2025, marks a crucial step in the European…
Following the October 15 announcement regarding the abandonment of the PPF development, the DGFIP and its partner AIFE are ramping…
Work with our team to build your ideal supply chain software stack and tailor it to your unique business needs.