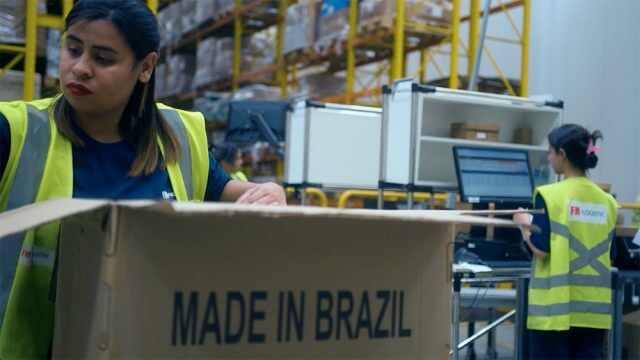
Generix WMS and FM Logistic Brazil simplify processes and increase efficiency in their 70,000 square meters of warehouses.
Transformation and Efficiency with Generix WMS Solution
Generix chooses Kyndryl to modernize IT infrastructure Read the press release
DHL is the global market leader in air freight, road transport and international express transport. It is also the No. 1 in ocean freight and contract logistics. DHL offers a complete range of customized solutions, from express document delivery to supply chain management.
DHL Spain is the result of the merger of Guipuzcoana Euro Express, Danzas, and DHL in April 2003. They have an extensive network of branches (over 120) and employ more than 7,500 professionals. DHL Solutions is the DHL division for contract logistics, warehouse management and distribution.
In addition to basic procurement logistics operations, warehousing and sales logistics, DHL offers value-added services such as finishing, co-packing, price labelling, invoicing, order processing, sales promotion and financial services.
Context of the project
DHL has opted for the Warehouse Management Software (WMS) of Generix to implement the logistics activity of its client Heineken in the warehouse of its factory in Seville.
Heineken wanted DHL to optimize its logistics management in order to control the distribution of both the brand it manufactures and the other brands it markets: Amstel and Cruzcampo.
The Heineken factory in Seville has 30,000 m2 of warehouse space and aspires to be the most productive in Europe, fulfilling an ambitious expansion plan that will cover beer distribution in southern Spain.
Aim of the project
The WMS should provide solutions in all areas of the logistics activity from the receipt of goods to the dispatch of the same, through the management of the stock in the different states of the same.
DHL wanted to streamline, optimize and manage all warehouse operations so that its client could know the status of its stock at all times, controlling the batches and expiry dates, the operations carried out and their quality level. The warehouse also had to manage the containers returned to the factory for reuse.
Finally, this warehouse was to receive and dispatch the transfer of goods between the different Heineken factories in Spain.
Developed Solution
In order to increase operational efficiency and speed, the radio frequency module of the Warehouse Management System was implemented in the receiving, storage bin and picking operations. In this way the warehouse operators can access the processes from the place where they are working, speeding up the automated results of reception, location and preparation and being able to enter the data of goods, locations and preparation supports through the reading of barcodes.
The implementation of the radiofrequency in the WMS has allowed the scenarios of reception directly from the factory, from other suppliers and all the containers and packaging (pallets) for the factory, as well as the transfer between factories in an agile way and minimizing errors, automatically assigning each product and knowing in real time the stock situation.
In the reception of the goods directly from the factory, we work with the reading of the EAN128 label code that it generates, validating it and automatically launching the location processes.
On the other hand, there is another radio frequency scenario for the rest of the receptions, in this case the logistics solution that the Warehouse Management Software provides for this type of reception is defined by the data capture through the scanning of the EANs of the different products.
The graphical configuration of the warehouse surface, which allows the Warehouse Management Solution, has achieved the optimized location of the goods in an open space or “mass areas” that has 90% of the Heineken warehouse by using an ADM space equivalence table and barcode location labels that delimit the physical space. The remaining 10% works with conventional racking, which is used as a picking area.
In the preparation of customer orders, the ability of the Warehouse Management System to perform a retail operation, as well as to combine the preparation of full and heterogeneous pallets, through processes that are served from various radio frequency scenarios, allows DHL Heineken to distribute the goods appropriately according to its typology of customers: wholesalers and retail stores.
The output of the goods in the WMS generates the electronic exchange of documents, which is integrated into Heineken‘s commercial management ERP.
Benefits obtained
El pilotaje de las operaciones en tiempo real, la optimización del espacio de almacén y la mejora de la calidad de servicio por la minimización de errores y tiempos de operación además de la trazabilidad total ofrecida por el Solución de Gestión de Almacén permitiendo a DHL optimizar toda la organización del almacén de forma que cumpla ampliamente los requerimientos que exige su cliente Heineken para el suministro de su red de distribución.
The piloting of operations in real time, the optimization of warehouse space and the improvement of the quality of service by minimizing errors and operation times in addition to the total traceability offered by the Warehouse Management Solution allow DHL to optimize the entire warehouse organization in a way that meets the requirements of its customer Heineken for the supply of its distribution network.
Find the full description of the solutions presented in this case study
Transformation and Efficiency with Generix WMS Solution
Since 1922, Shorr Packaging Corp. has established itself as a major player in packaging in the United States. Faced with…
Emballages Carrousel, a leader in packaging solutions, embarked on an ambitious project to modernize its operations and meet the growing…
Work with our team to build your ideal supply chain software stack and tailor it to your unique business needs.