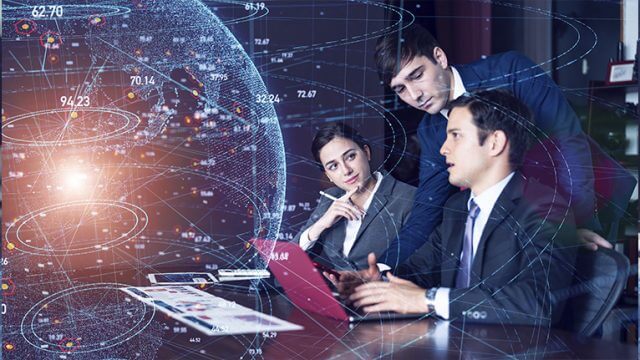
E-Invoicing and Its Geopolitical Stakes
France’s electronic invoicing reform relies on a Y-architecture, where Partner Dematerialization Providers (PDPs) play a central role in issuing and…
Generix Delivers Schematron for Electronic Invoicing to AFNOR to Ensure Interoperability Between PDPs Read the press release
Transportation delays are one of the consequences of supply chain congestion. For example, merchant ships delivered their cargoes later than ever in 2021: at the low point in March, only 40% of them were on time. These difficulties have hampered the efforts of distribution companies who were hoping to take advantage of an upturn in consumption, following the various confinements due to Covid-19. Ship capacity is limited due to significant global resupply. Another consequence? Rising shipping costs, with freight rates climbing at record speed. Land transportation is facing the same challenges.
Shared Supply Management (SSM), also called “pooling“, offers an intelligent response to these bottlenecks: unlike Shared Supply Management (SSM), it adds to the collaboration between manufacturers and traders, a collaboration between the manufacturers themselves. Manufacturers collaborate with the aim of sharing and reducing individual logistics costs. To be deployed effectively, the concept of SSM also requires the implementation of an integrated information system shared between the various parties (manufacturers, traders, carriers, warehousemen, etc.).
It allows for an economy of scale on storage costs. It brings more agility and efficiency in the operation, but also a better inventory management. Pooling is even simpler for manufacturers working on the same product range, sharing all or part of their customer base and/or following a similar logistic scheme. They share common storage constraints depending on the type of product sold.
SSM will reduce costs. For example, we can go from 20 platforms and 20 different trips to a single platform and a single trip. This will significantly reduce the carbon footprint. The “partners” can decide to share the trucks according to a fixed distribution (each has a number of pallets known in advance) or according to a variable distribution. The manufacturer will also have full visibility on sales and stocks and will thus be able to better control the rotation and assortment of its products. For distributors, SSM allows them to make real savings while making their product available at the right time, in the right department and for the right person. And thus respond to a customer who is more and more difficult to satisfy.
It is difficult to pool your transport without using a dedicated service provider, such as a 3PL company. In this case, a lack of visibility on the operations delegated to subcontractors can have dramatic consequences on your image as well as on your customer relations. To improve the visibility of your customers, Generix 3PL Portal offers many functionalities allowing you to consult the available stocks to date, to follow customer orders and replenishments, movements in real time and products according to different segmentation that you define (batches, dates…)
The SSM solution, Generix Collaborative Replenishment, reinvents shared supply management by increasing user productivity and business performance and by taking advantage of new technologies (cloud, analytics, RPA and deep learning).
Thanks to its various features:
More benefits with the Supplier Portal (P2P) solution, which digitalizes your supplier and service provider collaboration. It enables you to improve process and service level performance, reduce inventory, shortages, and disputes, improve S&OP and logistics operations efficiency, and increase sales volumes.
It reduces the operating cost of your processes by 20 to 40% while lowering the costs of referencing, order processing, logistics dispute management, inventory management, transportation, invoicing, payment… Finally, it allows you to create new value offers through collaboration.
France’s electronic invoicing reform relies on a Y-architecture, where Partner Dematerialization Providers (PDPs) play a central role in issuing and…
The B2B mandate in Germany, set to take effect on January 1, 2025, marks a crucial step in the European…
Following the October 15 announcement regarding the abandonment of the PPF development, the DGFIP and its partner AIFE are ramping…
Work with our team to build your ideal supply chain software stack and tailor it to your unique business needs.