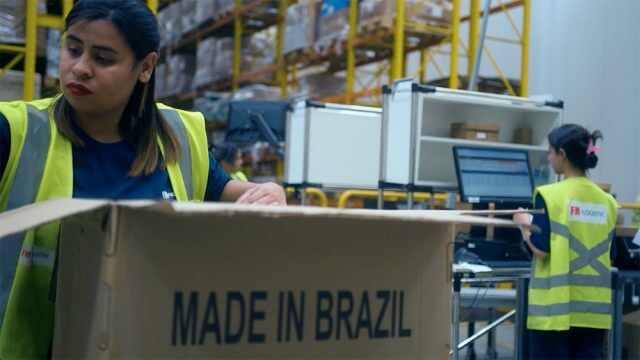
Generix WMS and FM Logistic Brazil simplify processes and increase efficiency in their 70,000 square meters of warehouses.
Transformation and Efficiency with Generix WMS Solution
Generix Delivers Schematron for Electronic Invoicing to AFNOR to Ensure Interoperability Between PDPs Read the press release
Nestlé is the world’s largest food and beverage company and its headquarters are in the Swiss town of Vevey, where it was founded more than 150 years ago. It is present in 186 countries around the world and its 276,000 employees are committed to Nestlé’s purpose of developing the power of food to improve the quality of life for all, today and for future generations. Nestlé offers a broad portfolio of products and services for people and their pets throughout their lives. Its more than 2,000 brands range from global icons like NESCAFÉ or NESPRESSO, to widely recognized locally manufactured brands like CERELAC, NESTUM and SICAL, among many others. The Company’s performance is guided by its Nutrition, Health and Wellness strategy and underpinned by strong commitments to the environmental sustainability of all its operations, where the ultimate goal is to achieve Net Zero by 2050. To meet this roadmap, Nestlé is focused on advancing regenerative food systems at scale, involving its entire value chain.
In Portugal, Nestlé is present since 1923 and currently has 2,347 employees, having generated in 2021 a turnover of 625 million euros. It currently has two factories (Porto and Avanca), a distribution center (Avanca) and five commercial branches spread over the mainland and the islands.
The size of Nestlé Portugal, the large product portfolio, the different business areas and the high number of customers require the adoption of administrative management processes that are fast, efficient and minimize the probability of errors and failures in information flows, exchanged on a daily basis between the company and its suppliers and customers.
These were some of the reasons that led the company, early on, to adopt technological solutions that enabled it to create the agility required to remain a leader of his sector. It was with this objective in mind that Nestlé Portugal adopted Generix EDI and Electronic Invoicing solutions for electronic document transactions with retailers and other business partners.
“The use of EDI in Nestlé has significantly improved the documents and information exchange process with all customers with whom we implemented this system. As a result, the whole process has become faster, standardized, more agile and much safer, which often benefits the trust relationship between Nestlé and these customers… In addition, EDI has also helped reduce errors usually caused by manual processes and as a result we have reduced bureaucracy and costs,” Luís Silva IT – System Analyst/Business Analys Nestlé Portugal
Order to dematerialize documents and facilitate information exchanges
In the late 90s Nestlé Portugal implemented the Generix EDI solution for the electronic transmission of documents – such as orders, invoices and delivery notes.
Through EDI it’s possible to exchange electronic documents, in a standard format, between the different information systems of the partners with whom Nestlé maintains commercial relations. This way, the company can quickly send and receive documents with its customers and suppliers, with maximum security, and the data is automatically integrated into its ERP. The whole process is carried out in 3 steps: document preparation, message translation into EDI format and documents transmission to the partner.
In 2006, the company took another step forward streamlining processes with the electronic invoicing solution implementation. This tool allowed Nestlé to improve the invoice handling process and increase productivity levels.
The confidence placed in Generix solutions, for more than two decades, proves the reliability and robustness of these tools over time. This demonstrates Nestlé’s Portugal innovative vision, which implemented, on time, its process digitalization and the modernization of information flows.
The post-pandemic context has emphasized the need of a digital transformation path and digitization process for the business competitiveness and efficiency.
Key benefits identified by Nestlé Portugal
Find the full description of the solutions presented in this case study
“The use of EDI in Nestlé has significantly improved the documents and information exchange process with all customers with whom we implemented this system. As a result, the whole process has become faster, standardized, more agile and much safer, which often benefits the trust relationship between Nestlé and these customers… In addition, EDI has also helped reduce errors usually caused by manual processes and as a result we have reduced bureaucracy and costs,”
Luís Silva
IT – System Analyst/Business Analys, Nestlé Portugal
Transformation and Efficiency with Generix WMS Solution
Since 1922, Shorr Packaging Corp. has established itself as a major player in packaging in the United States. Faced with…
Emballages Carrousel, a leader in packaging solutions, embarked on an ambitious project to modernize its operations and meet the growing…
Work with our team to build your ideal supply chain software stack and tailor it to your unique business needs.