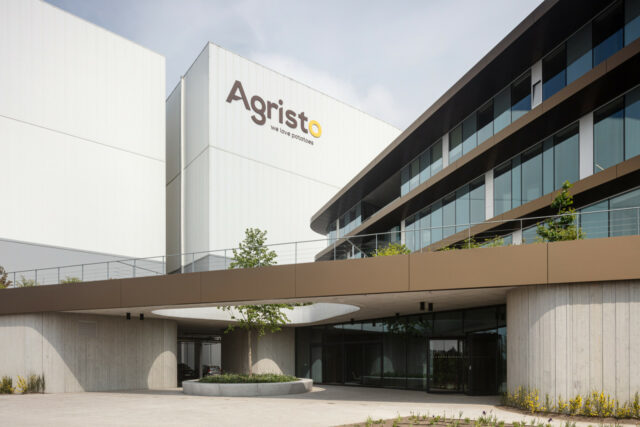
Success Story – AGRISTO BENELUX
A Potato Story at the Heart of Digital Flows
Raphaël Sanchez Appointed President of Generix Group. View the press release.
Volkswagen’s new strategy for the sale of original spare parts, PRO Service, is born with a priory objective. “ZERO mistakes” To this end, the agility and service requirements of the workshops were taken into consideration, such that it is predicted that in the next two years, PRO Service will have 41 interlinked warehouses throughout Spain, which will make it possible for any of their 845,000 group vehicle parts to be delivered within 2 hours, depending on the route, and with a goal of up to 4 deliveries per day.
The automotive company’s firm belief in the system is evidenced by its forecast that it will call on 400 professionals for this service, of whom fifteen engineers, to assist the repair technicians.
We are standing before a change in the distribution model for part which, without a doubt, will require the support of a technology partner to provide a solution for this innovative distribution strategy in the automotive sector.
Volkswagen has placed its trust in Generix for their WMS for its robustness and reliability and demonstrated by being fully operational in more than 1,100 warehouses in 30 countries.
Generix’s vast experience has made it possible to design warehouse flows, while optimising warehouse flows depending on the product and end customer.
This WMS is integrated in the client’s ERP to rapidly and securely integrate every type of orders managed in PRO Service.
Likewise, this connectivity allows Volkswagen to get confirmation in real time for both buy and sell orders, as well as the adjustments performed in the warehouses, and a complete stock view.
To design better logistics processed based on the requirements of each order, client and part, both in receiving and preparation of orders.
To design the warehouses with dynamic picking management and optimised location according to product turnover and size.
Automated planning of order preparation based on blow (urgent, stock and display).
Increase in service quality thanks to the internal controls performed by the WMS in the various system processes.
Reliability of warehouse stock thanks to rotating inventories and continuous counting during preparation
Find the full description of the solutions presented in this case study
A Potato Story at the Heart of Digital Flows
Major player in the agri-food industry, Nestlé, has been relying on Generix Group’s solutions for digitalizing processes for two decades
The BEL Group Chooses Generix Collaborative Replenishment Solution in SaaS for its Supply Operations with all its Retail Clients
Work with our team to build your ideal supply chain software stack and tailor it to your unique business needs.